Spot welding is a powerful tool used to quickly and efficiently join metal components together. It involves the use of a special machine that applies an electric current to two metal surfaces. The intense heat created from the electrical current melts and fuses the two surfaces together, creating a strong bond that can last for years. Spot welding machines are easy to use and require minimal setup time, making them ideal for both industrial and home use. With the right machine, you can weld metal with confidence, knowing that your welds will be strong and reliable. Spot welding is a great way to create strong metal welds quickly and easily.
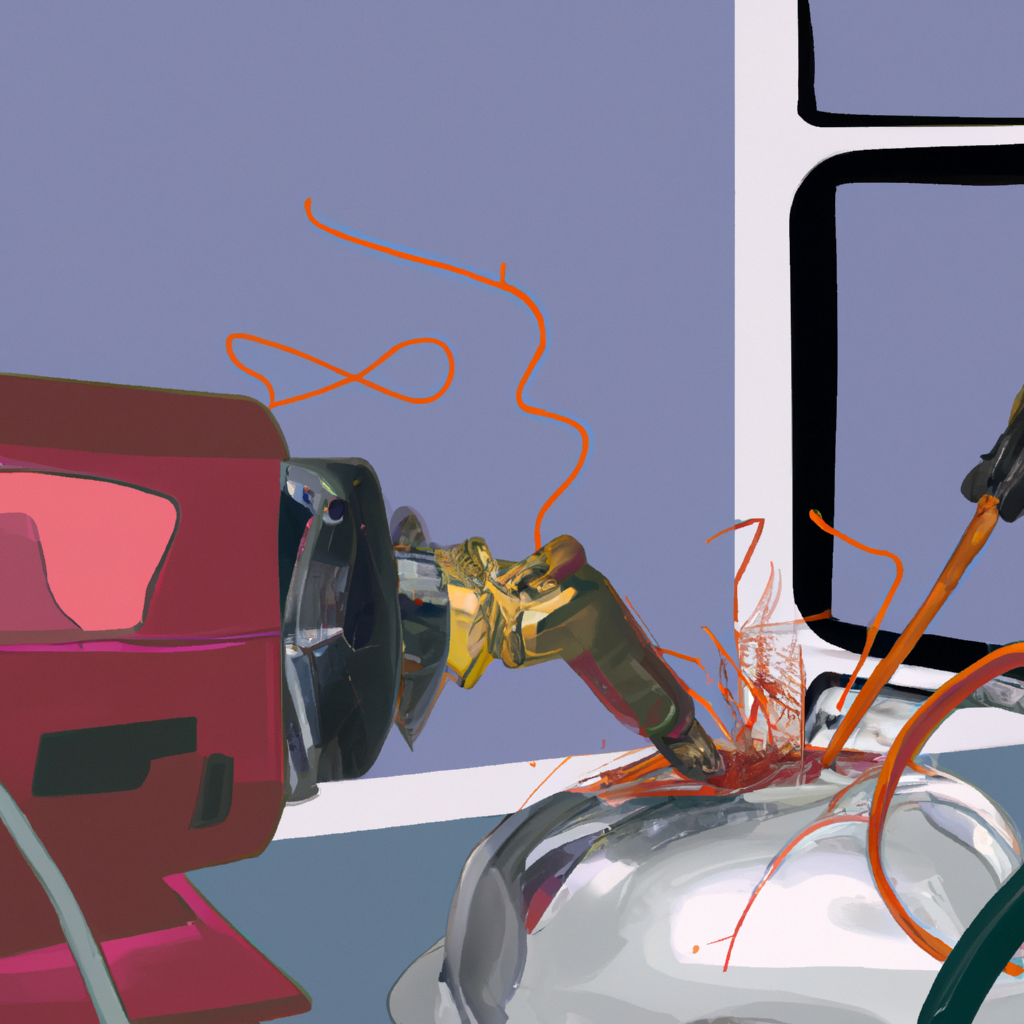
What is a Spot Welding Machine?
A spot welding machine is a specialized type of welding machine used to join two or more metal surfaces together. It is typically used to join pieces of sheet metal, but can also be used to join other metals such as aluminum or stainless steel. The spot welding machine works by applying pressure and an electric current to the metal surfaces, creating a strong bond between them.
The spot welding machine usually consists of two electrodes, a transformer, and a welding gun. The transformer supplies a low-voltage current, usually between 15 and 40 volts, to the electrodes. The current is applied to the electrodes, which heat up the metal surfaces. The heat melts the metal, creating a bond between the two pieces. The electric current is maintained for several seconds, allowing the bond to set.
The welding gun is used to apply pressure to the metal surfaces. This helps to ensure that the two pieces are firmly pressed together, creating a strong bond. The spot welding machine also has a timer, which is used to control the duration of the welding process. The timer ensures that the metal is heated for the optimal amount of time, creating a strong and lasting bond.
Spot welding is a simple and reliable method of joining two or more metal surfaces together. It is quick, efficient, and produces a strong bond. Spot welding machines are widely used in the automotive, aerospace, and construction industries.
How Does a Spot Welding Machine Work?
A spot welding machine uses two metal electrodes to join two pieces of metal together. The electrodes apply pressure and heat to the metal pieces, creating an electric arc that melts the metals at the point of contact. This creates a welded joint that is strong and secure.
The spot welding machine uses a transformer to create an electrical current that passes through the electrodes. This current creates heat in the metal pieces, which melts the metal and creates the weld. The transformer can adjust the temperature and current to create the perfect weld.
The machine also uses a timer to measure the length of time the current passes through the electrodes. A longer welding time will create a stronger weld. It is important to find the right balance between the current, temperature, and welding time to create the strongest weld.
Spot welding machines are used in many industries, including automotive, aerospace, electronics, and construction. They are used to join thin sheets of metal together in a quick and efficient manner. They are also used to create strong and secure welds that are difficult to create with traditional methods.
What Are the Components of a Spot Welding Machine?
A spot welding machine is a device used to join metal sheets together by fusing them with electric current. It works by using two copper electrodes to pass an electric current through the metal, which causes the metal to heat up and melt. The melted metal forms a bond between the two pieces of metal, creating a strong weld. Spot welding machines are used in a variety of industries, from automotive manufacturing to sheet metal fabrication.
The components of a spot welding machine include a power source, electrodes, a transformer, a timer, a cooling system, and a welding controller. The power source is usually an electric power grid, but may also be a battery or generator. The electrodes are usually made of copper and are connected to the power source. The transformer converts the power source into an appropriate voltage and current for welding. The timer is used to control the amount of time each weld is applied. The cooling system is used to cool down the electrodes after each weld. The welding controller is used to regulate the welding parameters, such as current, voltage, and time.
Spot welding machines are essential for many manufacturing processes and are used to create strong, reliable welds. By understanding the components of a spot welding machine and how they work together, you can ensure that your welds are strong and reliable.
What Are the Benefits of Using a Spot Welding Machine?
Spot welding machines are used to securely join two or more pieces of metal together. This process is done by applying pressure and an electrical current to the two pieces of metal. The electrical current causes the metal to heat up and form a strong bond between the two pieces. The spot welding machine has numerous advantages over other methods of joining metal together.
One of the major benefits of spot welding machines is their speed. Spot welders can quickly and efficiently weld two pieces of metal together in a fraction of the time it would take to use other methods. This can save both time and money for businesses that use spot welders in their operations. Spot welders are also cost-effective. Spot welding machines are relatively inexpensive when compared to other welding machines. They also require little maintenance, which can help businesses save money in the long run.
Spot welding machines are also safe to use. The electrical current used in the welding process is kept at a low level, making it safe to use. The pressure applied to the metal pieces also helps keep the welding process safe.Spot welding machines are also very versatile. They can be used to weld many different types of metals, including stainless steel, aluminum, and copper. This makes them ideal for a wide variety of welding applications.
Spot welding machines offer many advantages over other welding methods. They are fast, cost-effective, safe, and versatile. Spot welding machines can help businesses save time and money while producing strong and reliable welds.
How Do Different Types of Spot Welding Machines Operate?
Spot welding machines use electrodes to weld two or more pieces of metal together. The machine focuses an electrical current onto a small area between the two pieces of metal, causing the metal to heat up and melt. This creates a bond between the two pieces of metal. There are several types of spot welding machines, each with its own unique set of features.
Projection spot welders use two electrodes to create a weld. The electrodes are mounted on a frame that is moved to the desired spot. The electrodes are then pressed together, and the current is focused onto the area between them. The current causes the metal to heat and melt, creating a weld.
Resistance spot welders use a single electrode mounted on a rotating arm. This arm is moved over the area to be welded, and the current is focused onto the area. The current causes the metal to heat and melt, and the arm rotates to ensure that the weld is even. This type of welding is ideal for welding thin sheets of metal.
Micro spot welders use several electrodes to create a weld. The electrodes are mounted on a frame and the current is focused onto the area between them. This type of welding is very precise and can be used to weld thin sheets of metal together.
Spot welding machines are an essential tool for many industries. There are several types of spot welding machines available, each with its own unique set of features. By understanding how each type of machine operates, you can choose the best one for your needs.
What Factors Should be Considered Before Using a Spot Welding Machine?
When using a spot welding machine, several factors should be taken into consideration. First, what type of project are you working on? Spot welding machines come in a variety of sizes, shapes, and power levels. It is important to select the right machine for the job. Second, what type of material are you welding? Different materials require different power levels. Additionally, some materials may require additional steps to ensure a successful weld.
Third, what is the size of the material you are welding? Larger materials or thicker materials require more power from the welding machine. Fourth, what is the distance between the two pieces of material? This is an important factor as the distance affects the amount of current needed for a successful weld. Lastly, what is the amperage of the welding machine? Amperage is the amount of current the machine can disburse, and it is important to choose the right amperage for the job.
What Safety Precautions Should be Taken Before Using a Spot Welding Machine?
Before using a spot welding machine, safety precautions should be taken to prevent potential accidents and injuries. First, make sure to wear protective gear such as safety glasses, gloves, and a face shield. This will protect your eyes, hands, and face from the sparks that are created during the welding process.Second, ensure that the welding area is clear of any combustible materials that could catch fire. Also, check the machine for any loose wires or connections that could create a spark.
Third, make sure to keep your hands and clothing away from the welding area as these could become caught in the machine and cause injury. Fourth, be aware of the power source and make sure it is properly connected to the machine. Also, make sure to use the appropriate power cord for the welding machine.Finally, ensure that the machine is properly grounded and that all of the connections are secure. This will help to prevent shock hazards and potential fires. By following these safety precautions, you can help to ensure the safe operation of your spot welding machine.
What Are the Most Common Issues with Spot Welding Machines?
Spot welding machines are highly reliable pieces of equipment, but some common issues can arise from time to time. These include corrosion of the electrodes, improper operation of the machine, incorrect power settings, improper grounding, and insufficient electrode pressure. Corrosion of the electrodes can be caused by insufficient cleaning, as well as exposure to moisture or other contaminants. Improper operation of the machine can cause the electrodes to be incorrectly positioned, leading to poor welds. Incorrect power settings can also result in incomplete welds or inadequate penetration. Improper grounding can lead to arcing, resulting in poor welds as well. Finally, insufficient electrode pressure can lead to inadequate welds.
How spot welding machine works? Spot welding machines use two electrodes to apply pressure and electrical current to two pieces of metal. The electrodes heat the metal, causing them to melt and fuse together. The heat is generated by the resistance of the metal to the flow of electric current. The amount of current and pressure applied to the metal determines the strength of the weld. If done correctly, spot welding can create a strong, durable bond between two pieces of metal.
How Can Spot Welding Machine Maintenance Be Performed?
Spot welding machine maintenance is an important part of ensuring that the machine performs at its highest potential. Proper maintenance can help extend the life of the machine, reduce downtime, and lower repair costs. Here are some tips for maintaining a spot welding machine:
- Clean the machine regularly. It is important to keep the machine clean in order to maintain its functionality. Use a soft cloth and a mild detergent to wipe down the machine. Make sure to get into all the nooks and crannies.
- Check the power supply and connections. Make sure all connections are secure and that the power supply is functioning properly. If there are any loose connections, make sure to tighten them.
- Monitor the welding process. Regularly check the current, voltage, and welding time to ensure that the welding process is running correctly. This will help you identify any problems before they become major issues.
- Perform scheduled maintenance. Regularly inspect and replace worn parts as necessary. This includes the welding electrodes, contact tips, and other components that are subject to wear and tear.
- Calibrate the machine. To ensure accuracy and consistent results, it is important to frequently calibrate the machine. This will help ensure that the welding parameters remain consistent.
By following these tips, you can help keep your spot welding machine running at its best. Regular maintenance will help the machine last longer and reduce costly repairs.
How Long Does a Spot Welding Machine Last?
A spot welding machine is a type of welding machine used to weld two work pieces together. It works by applying pressure and electrical current to the two pieces of metal, often steel, to fuse them together. The current passes between the two pieces of metal, causing the molecules to heat up and bond together.
The life expectancy of a spot welding machine depends on its use and care. Generally, a machine can last up to 10 years when properly maintained. The welding rods, tips, and cables should be regularly inspected and replaced as needed. It is also important to make sure the machine is used in the proper environment and with the correct welding parameters.
Spot welding machines are often used in the automotive industry to join two pieces of metal together quickly and efficiently. They are also used in the manufacturing industry to join metal parts together. Spot welding machines can be used to weld several kinds of metals, including stainless steel, aluminum, and brass.
Spot welding machines are an essential part of many industries, and with proper care and maintenance, they can last for many years. Regular maintenance and proper usage are key to ensuring a spot welding machine lasts for the full 10 years or more.