Welding is one of the most critical techniques used in a wide variety of industries, from automotive to aerospace. Quality assurance in welding is essential for ensuring the safety and reliability of the finished product. Inspecting the welding quality requires a keen eye and detailed knowledge of the welding process. In this article, you’ll learn the basics of welding quality inspection, from visual and non-visual techniques to the most advanced methods. We’ll also discuss how to identify common welding defects and how to ensure the highest quality welds. With this knowledge, you’ll have the confidence and skills to ensure that your welds are of the highest quality.
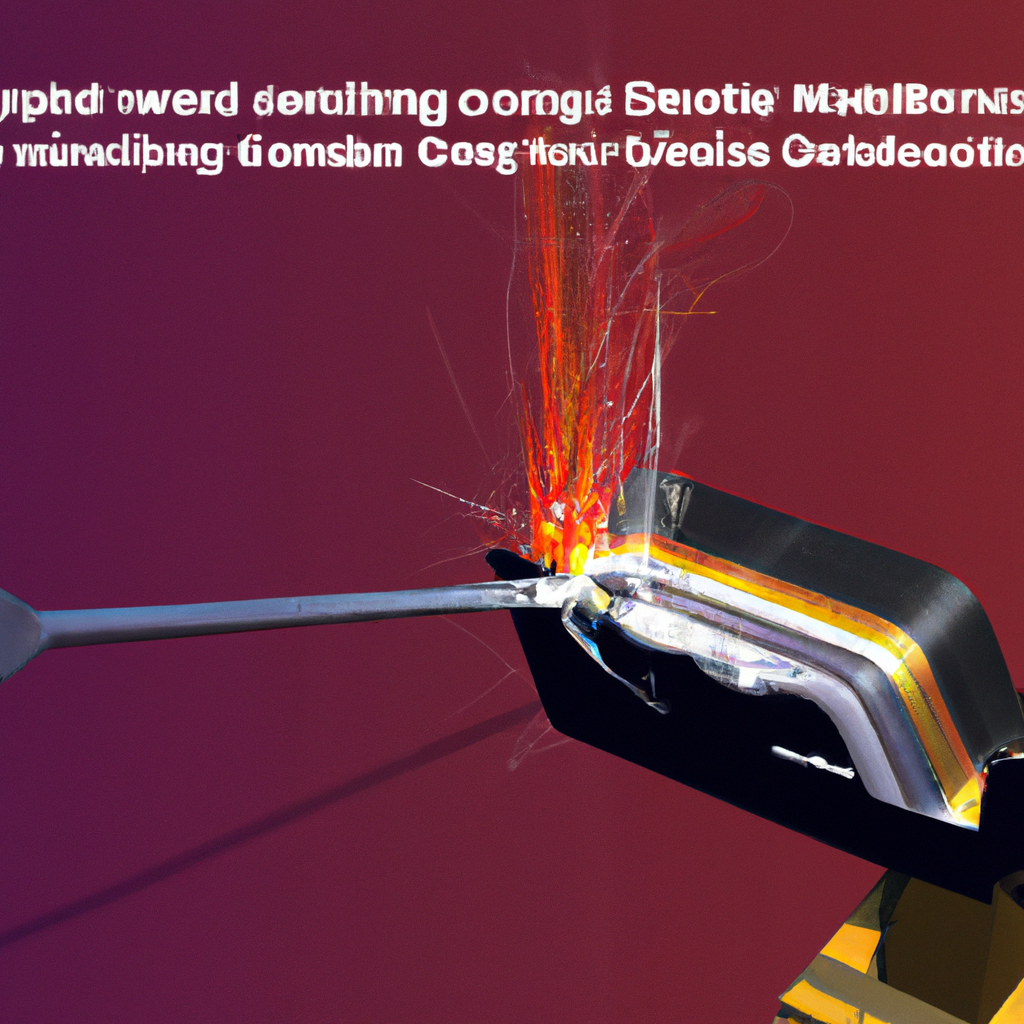
What are the Types of Welding and How Can They be Inspected?
Welding is a process used to join two or more materials together. It involves the application of heat and pressure to create a strong bond between the pieces. There are several types of welding, each requiring different techniques and materials. These include:
- Gas Welding: Uses a flame to heat and melt the metal. This type of welding is typically used to weld light metals such as aluminum and copper.
- Arc Welding: Uses an electric current to heat and melt the metal. This type of welding is used for heavier metals such as steel.
- MIG Welding: Uses a wire feeder to feed a wire into the weld. This type of welding is primarily used for welding aluminum and steel.
- TIG Welding: Uses a tungsten electrode to heat and melt the metal. This type of welding is used for thin metals such as stainless steel.
- Spot Welding: Uses electric current to create an electrical arc between two pieces of metal. This type of welding is used to join two pieces of sheet metal together.
In order to ensure the quality of a weld, it must be inspected. Visual inspection is the most common way to inspect a weld. This involves looking at the weld to check for any cracks, porosity, incomplete fusion, or any other defects. Non-destructive testing (NDT) is also used to inspect a weld. This type of testing uses techniques such as ultrasound, radiography, magnetic particle, and eddy current to detect flaws in the weld.
What are the Common Defects in Welding and How Can They be Detected?
Common defects in welding include warping, cracking, porosity, lack of penetration, and undercut. These defects can be detected through several methods:
- Visual inspection: By closely examining the welded joint and surface for any imperfections.
- Magnetic particle testing: By detecting any discontinuities in the material with the help of a magnetic field and magnetic particles.
- Radiographic testing: By using X-ray or gamma rays to detect any internal discontinuities.
- Ultrasonic testing: By using high-frequency sound waves to detect any internal discontinuities.
- Penetrant testing: By using a penetrant material which is applied to the surface and then examined for any defects.
These methods can be used to detect any welding defects and ensure the quality of the welded joint.
What are the Visual and Non- Destructive Testing Methods Used to Inspect Welds?
Visual and Non-Destructive Testing (NDT) methods are used to inspect welds for their quality and integrity. Visual inspection involves the use of human eyes to check for surface defects in welds, while NDT methods use specialized equipment such as ultrasonic, radiographic, magnetic particle, and eddy current testing.
Visual inspection can detect surface defects such as porosity, cracks, and poor surface finish. It can also detect defects in the weld shape, such as undercut, overlap, and lack of fusion. It is the most common method used to inspect welds, as it is cost-effective and does not require the use of specialized equipment.
NDT methods can detect surface and subsurface defects that may not be visible to the naked eye. Ultrasonic testing uses ultrasounds to detect flaws in welds, while radiography uses X-rays or gamma rays to detect subsurface defects. Magnetic particle testing uses magnetic fields to detect discontinuities, while eddy current testing uses electric current to detect surface defects.
When inspecting welds, it is important to ensure that they are free of any defects that may compromise the integrity of the structure. Visual and NDT methods can be used together to ensure that welds are of the highest quality.
How Can Metallurgical Testing be Used to Inspect Welds?
Metallurgical testing can be used to inspect welds by evaluating the welded material for its strength, integrity, and hardness. The following are some of the methods used in metallurgical testing:
- Visual inspection – examining the weld joint for any defects
- Macro-etch testing – examining for any micro-structural changes in the weld material
- Hardness testing – determining the hardness of the weld joint
- Magnetic particle testing – detecting any magnetic flaws in the weld joint
- Radiography testing – examining the weld joint for any internal defects
- Ultrasonic testing – checking for any cracks in the weld joint
These tests can be conducted to ensure that the welds are free from any defects, and that they meet the required standards of strength and integrity. The results of the metallurgical testing can then be used to determine the quality of the welding, and any necessary repairs or modifications can be made.
What are the Benefits of X-Ray Testing for Weld Quality?
X-ray testing is a useful tool for inspecting weld quality. It offers several benefits, including:
- Non-destructive testing: X-ray testing does not require cutting or damaging the weld in any way, allowing for the weld to be reused without further damage.
- Highly accurate: X-rays allow for precise measurements and can detect a wide range of flaws, including cracks, pores, and other defects that would be difficult to spot with the naked eye.
- Time-saving: X-ray testing is fast and efficient, allowing for quick inspections with minimal effort.
X-ray testing can help to ensure that all welds meet quality standards and are safe and reliable. It is important to remember that X-ray testing is only one method of inspecting weld quality and should be used in conjunction with other methods, such as visual inspections, to ensure the highest level of accuracy.
What is the Purpose of Magnetic Particle Testing for Weld Quality?
Magnetic particle testing is a method of testing welds to ensure their quality. It is a non-destructive testing method that can be used to detect surface and subsurface defects in a weld. It works by introducing a magnetic field into the weld, which causes particles of iron or steel to become magnetically charged and cling to any cracks or other defects in the weld. This makes it an ideal method for inspecting welds for defects, as it is quick, non-destructive, and relatively inexpensive.
To inspect welding quality using magnetic particle testing, the following steps should be taken:
- Clean the weld and the area surrounding it.
- Apply a magnetic particle solution to the weld.
- Introduce a magnetic field into the weld using either an electromagnet or a permanent magnet.
- Examine the weld under a black light or UV light to detect areas where the magnetic particles have adhered to any cracks or other defects.
By using magnetic particle testing, welders can quickly and easily inspect welds for defects, ensuring that the welds are of the highest quality.
What are the Advantages of Ultrasonic Testing for Weld Quality?
Ultrasonic testing is a reliable and efficient method for inspecting weld quality. It has several advantages over other inspection techniques, such as:
- It is non-destructive, meaning the component being inspected does not have to be damaged or altered in order for the inspection to take place.
- It is fast, accurate, and highly sensitive, making it ideal for detecting even small defects.
- It can be used on a variety of materials, including metals, composites, and ceramics.
- It can be used to check the internal structure of the weld, such as porosity, inclusions, and cracks.
- It can detect defects in welds that are not visible to the naked eye.
Ultrasonic testing is becoming increasingly popular for weld quality inspections due to its reliability and accuracy. It is a cost-effective way to ensure that welds are free of defects, and that they will provide the desired level of performance.
What are the Different Types of Eddy Current Testing and How Can They be Used for Weld Quality Assurance?
Eddy current testing is a non-destructive method used to inspect welds for surface and sub-surface flaws. It can be used to detect cracks, porosity, inclusions, and other defects in welds and can be used for quality assurance of welds. There are several types of eddy current testing that can be used for weld quality assurance, including:
- Pulse Eddy Current Testing (PECT): PECT uses an alternating current signal to detect flaws such as cracks, porosity, and inclusions. It can detect surface and subsurface flaws and can be used to inspect both ferrous and non-ferrous materials.
- Alternating Current Field Measurement (ACFM): ACFM uses an alternating current field to detect flaws. It is often used for welds in pipelines and can detect surface and subsurface flaws in both ferrous and non-ferrous materials.
- Magnetic Flux Leakage (MFL): MFL uses a magnetic field to detect flaws in ferrous materials. It is often used for welds in pipelines and can detect both surface and subsurface flaws.
Eddy current testing can be used to inspect welds for surface and subsurface flaws and can be used for quality assurance of welds. It is a non-destructive method and can detect a variety of flaws, including cracks, porosity, and inclusions. There are several types of eddy current testing that can be used for weld quality assurance, including pulse eddy current testing, alternating current field measurement, and magnetic flux leakage.
What are the Requirements for Welding Procedure Qualification?
Requirements for Welding Procedure Qualification:
- Ensure that welding equipment is properly set up and maintained.
- Check that the welding parameters are certified and checked.
- Check that the correct welding consumables are used.
- Monitor the welding process and document any changes.
- Conduct a visual inspection and non-destructive testing (NDT) of welds.
The results of these tests should be recorded in a welding procedure qualification record (WPQR) which will be used to determine if the welding process meets the requirements of the applicable code or standard.
What is the Role of Welders and Weld Inspectors in Ensuring Quality Welds?
Welders and weld inspectors both have a critical role in ensuring quality welds. Welders must use the correct materials, tools, and techniques to get the best weld possible. Weld inspectors then check for any flaws, defects, or discrepancies in the weld that may compromise the strength or integrity of the weld.
Welders must:
- Read and understand welding codes and specifications.
- Follow instructions from the welding procedure.
- Use the correct tools and materials for the job.
- Check their welds for quality and consistency.
Weld inspectors must:
- Perform visual inspections of welds.
- Perform non-destructive testing (NDT) such as x-rays, ultrasonic testing, or dye penetrant testing.
- Conduct destructive testing such as bend tests, tensile tests, or hardness tests.
- Report any discrepancies or flaws found during inspection.
By following these steps, welders and weld inspectors can help ensure quality welds that meet industry standards and customer expectations.
How Can Weld Quality be Monitored and Controlled?
Weld quality can be monitored and controlled by following the below steps:
- Inspecting the welds for any visible defects such as cracks, porosity, slag inclusions, undercut, etc.
- Testing the welds with the help of ultrasonic, radiographic, magnetic particle, and dye penetrant methods.
- Performing macro-examination of welds with the help of a microscope.
- Verifying the welds against the relevant welding codes.
- Conducting regular maintenance on the welding equipment.
- Ensuring proper joint preparation and welding parameters.
- Properly training the welding personnel.
- Using quality welding consumables.
What are the Different Qualification Tests for Welders and Welding Supervisors?
Qualification tests for welders and welding supervisors help to understand the competencies of welders and supervisors in the welding process. Generally, there are two types of tests:
- Welder Qualification Tests
- Welding Supervisor Qualification Tests
Welder Qualification Tests include:
- Visual inspection of weld
- Filler metal verification
- Welding technique
- Welding process
- Welding position
- Code compliance
Welding Supervisor Qualification Tests include:
- Welding procedure qualification
- Welding procedure specification
- Welding procedure test
- Welding procedure qualification record review
- Welding procedure qualification test report review
- Welding procedure specification record review
To inspect welding quality, welders and supervisors must perform visual inspections of the welds, verify the correct filler metal, and ensure that the welding techniques, process, and position comply with the applicable code. Additionally, welding supervisors should review the welding procedure qualification records, test reports, and welding procedure specifications.