A MIG welder is an incredibly versatile tool. With it, you can weld a variety of materials, from steel to aluminum to copper. With the right settings and techniques, you can weld sheet metal, cast iron, and even stainless steel. Additionally, you can create fillet welds, lap welds, and butt welds. MIG welding is a great option for those looking to do welding projects safely and quickly. So if you’re looking for a reliable welding tool, look no further than a MIG welder.
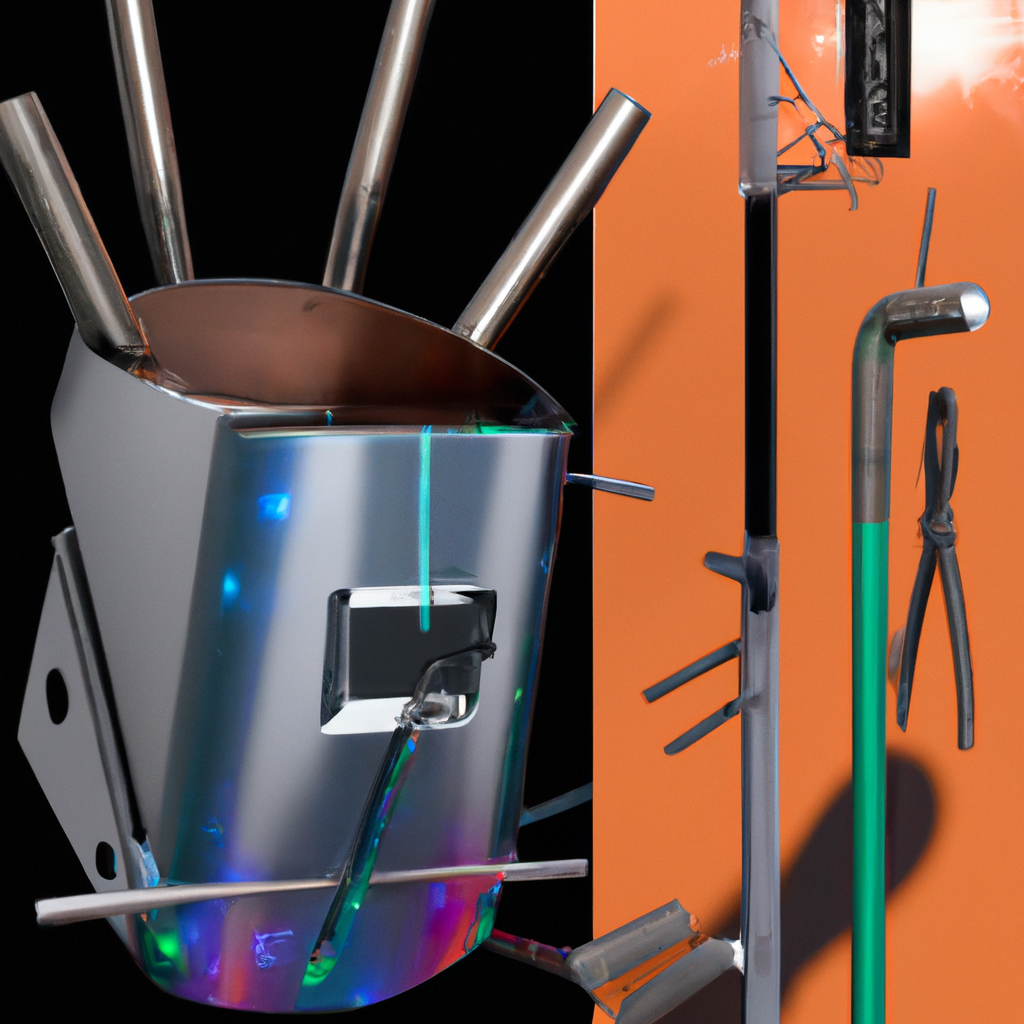
What is a MIG Welder?
A MIG welder is a type of welding machine that uses a consumable wire electrode and a shielding gas to join two pieces of metal together. It is a popular welding process for many different types of applications, such as home repairs, automotive and industrial projects.
What can you weld with a MIG welder? MIG welders are used to join many different types of metals, including aluminum, steel, stainless steel, and copper. They can be used for a variety of welding applications, such as:
- Fabrication of metal components and structures
- Welding of automotive and aircraft components
- Joining of large steel structures
- Repairing of broken or damaged metal parts
- Welding of thin gauge metals
MIG welders are also great for welding in tight spaces and for making precise welds. With the right equipment and a little practice, almost anyone can learn to use a MIG welder.
What Metals Can You Weld with a MIG Welder?
You can weld a variety of metals with a MIG welder, including:
- Mild steel
- Stainless steel
- Aluminum
- Cast iron
MIG welders can also be used with specialty metals such as:
- Nickel alloys
- Copper alloys
- Titanium
MIG welding is one of the most versatile welding processes, and it can be used to weld a wide variety of metals with different thicknesses and properties. The process is relatively easy to learn and can be used on both thin and thick materials.
What is the Process of Welding with a MIG Welder?
Welding with a MIG welder involves several steps:
- Set up the welder by connecting the ground clamp to the workpiece, then plugging in the power cable.
- Select the wire size and type based on the type of material being welded.
- Select the right welding settings depending on the type of material being welded.
- Load the wire into the feeder and adjust the wire speed according to the welding settings.
- Put on safety equipment such as a welding helmet, gloves and apron.
- Position the gun at the starting point and pull the trigger to start the arc.
- Move the gun in a steady motion, following the weld line.
- Release the trigger when finished welding.
- Inspect the weld for any flaws.
With a MIG welder, you can weld various metals such as steel, stainless steel, aluminum, and copper. The welder can also be used for repair and fabrication work.
What Materials are Required to Weld with a MIG Welder?
In order to weld with a MIG welder, a few materials are required. These include:
- MIG welding wire
- Welding electrodes
- Welding helmet
- Welding gloves
- Welding rod
- Ground clamp
- Gas regulator
- Gas cylinder
- Welding cable
In addition to the materials listed above, a MIG welder can weld many different types of metals, including steel, aluminum, stainless steel, and copper. MIG welders also require a power source, such as an electrical outlet or generator, in order to function properly.
What Safety Precautions Should Be Taken When Using a MIG Welder?
When using a MIG welder, it is important to take certain safety precautions to ensure a safe work environment. Here are some safety tips:
- Always wear the proper safety gear, including a welding helmet, welding gloves, and a leather apron.
- Make sure to keep the welding area well-ventilated and free of flammable materials.
- Inspect the equipment before use, and only use equipment in good working condition.
- Ensure the cables are properly grounded and the leads are connected correctly.
- Do not exceed the recommended welding current.
- Be aware of the location of the welding arc and the sparks it produces.
- Be aware of the weld area and keep other personnel out of the welding zone.
- After welding, allow the equipment to cool down before handling.
What can you weld with a MIG welder? MIG welders can be used to weld many different kinds of metals, including aluminum, steel, stainless steel, and magnesium. They can also be used for welding sheet metal, castings, and tubing.
What Types of Joints are Suitable for MIG Welding?
MIG welding is a popular form of welding that uses a metal inert gas (MIG) to establish an electric arc between a consumable wire electrode and the workpiece. This type of welding is ideal for welding many types of metals, such as steel and aluminum. Here are some of the types of joints that can be welded with a MIG welder:
- Butt joints
- Lap joints
- T-joints
- Corner joints
- Edge joints
- Flange joints
MIG welding is also well-suited for fillet welds, which are the most common type of joint used in fabrication. These welds are used to join two pieces of metal at a right angle, and can be used to attach two pieces of metal together in a variety of ways. MIG welding can also be used to create more complex welds, such as V-groove welds, U-groove welds, and J-groove welds.
MIG welding is an excellent choice for welding various types of joints due to its speed and versatility. With the right equipment and proper technique, MIG welding can be used to create strong, reliable welds in a variety of applications.
How Does the Wire Feed Rate Affect Weld Quality?
The wire feed rate is a key parameter that affects the quality of a weld. It controls the speed of the wire being fed into the weld joint, and too slow or too fast of a feed rate can negatively impact the weld strength, appearance, and overall quality.
A wire feed rate that is too slow will lead to a weak weld with poor penetration and can cause cold lapping. Cold lapping occurs when the weld metal does not have enough heat energy to penetrate the base metal, and can cause the weld to be weak and brittle. On the other hand, a wire feed rate that is too fast can cause porosity in the weld, which can lead to weaknesses in the weld joint.
In order to ensure optimal weld quality, it is important to maintain a consistent wire feed rate. The ideal feed rate will vary depending on the type of material being welded, the amperage being used, and the size of the wire being used. Generally, a wire feed rate of around 80-120 inches per minute is recommended for most welding applications.
Using a wire feed rate that is too slow or too fast can have serious consequences, so it is important to be aware of the proper feed rate and adjust it accordingly. With the right feed rate, you can achieve a strong weld with good penetration and a beautiful finish. With a MIG welder, you can weld a variety of materials, including steel, aluminum, stainless steel, and cast iron.
What is the Proper Technique for MIG Welding?
MIG (Metal Inert Gas) welding is a semi-automated welding process that relies on a welding gun, a power source, and a welding wire to create strong welds. Here’s the proper technique for MIG welding:
- Select the right welding wire for the job. Make sure it has the right diameter and type of wire for the job.
- Choose the right power setting for the job. It should be high enough to melt the wire but not so high that it creates spatter and sparks.
- Hold the welding gun at an angle of 10-15 degrees. This will ensure that the heat is concentrated on the joint.
- Move the welding gun in a steady, uniform motion. Moving it too quickly will create weak welds.
- Keep the nozzle of the welding gun at a distance of 1/8-1/4 inch from the joint. This will ensure that the weld is strong and evenly distributed.
- Allow the weld to cool before moving the gun away from the joint.
By following these steps, you can create strong, durable welds with a MIG welder. With a MIG welder, you can weld a variety of metals including aluminum, steel, stainless steel, and copper.
What are Some Common Problems Encountered When MIG Welding?
MIG welding is a popular welding process that is often used for projects involving metal construction. However, it is not without its challenges. Common problems encountered when MIG welding include:
- Incorrect welding parameters, such as current, voltage, travel speed, and wire feed speed.
- Incorrect wire type or diameter.
- Contamination of the welding area, such as rust or dirt.
- Improper joint preparation.
- Inadequate shielding gas flow.
- Incorrect joint design.
- Incorrect wire feed angle.
These problems can cause welds to be weak, have poor penetration, and have a rough appearance. To minimize these issues, it is important to use the correct welding parameters, wire type, and joint design for the application. Additionally, it is important to ensure that the welding environment is clean and free of contaminants, and that the joint is properly prepared.
What are Some Tips for Improving the Quality of MIG Welds?
Here are some tips for improving the quality of MIG welds:
- Choose the right wire and gas for the job.
- Ensure cleanliness of all the parts that will come into contact with the weld.
- Use the right welding parameters such as voltage, amperage and wire speed.
- Maintain a consistent arc length throughout the weld.
- Ensure proper joint preparation with the right gap and fit-up.
- Use an appropriate welding technique for the job.
- Use adequate shielding gas coverage.
- Keep the weld area free from contaminants such as moisture, rust or oil.
- Practice regularly and take regular breaks to avoid fatigue.
With the right preparation and technique, a MIG welder can be used to weld many different types of metals, including steel, aluminum, and stainless steel.