Are you facing issues of weak welds or welds that are not holding? Are you a welder struggling to find an answer to this question? You’re not alone! Many welders have faced these issues and this article will help you understand why your stick welds may not be holding. By understanding the underlying causes of weak welds, you can quickly identify and address the problem, so you can get back to your welding projects with confidence. Read on to discover the reasons why your stick welds may not be holding.
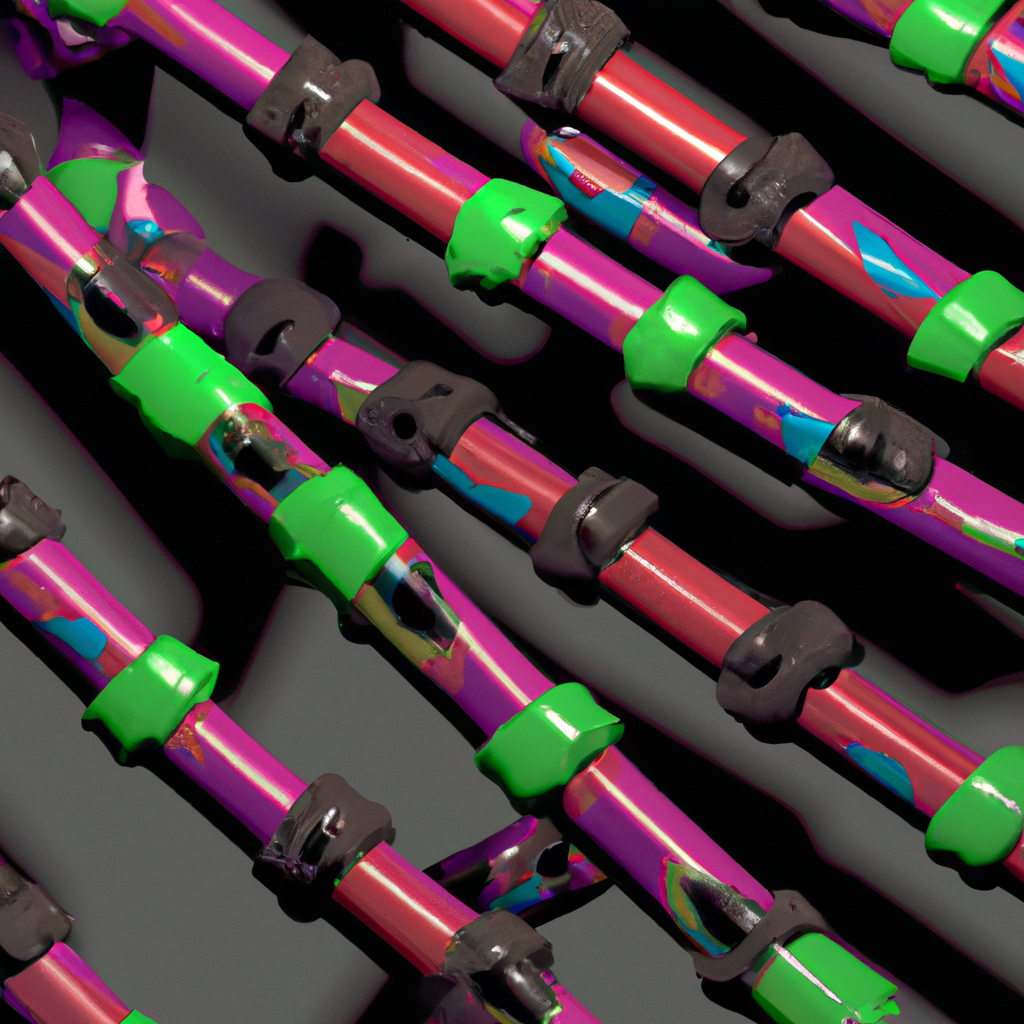
What welding process are you using?
I’m using a stick welding process to join two pieces of metal together. Unfortunately, my welds are not holding and I’m not sure why. Here are some potential causes of why my stick welds are not holding:
- The metal I’m trying to join together is too thick. Stick welding is not recommended for thick metals.
- There is too much heat in the weld area. High heat can cause the welds to weaken.
- The metal I am welding is not properly prepared. It should be cleaned and degreased before welding.
- The welding rod I’m using is not the right type for the material I’m welding. Different metals require different welding rods.
- I’m not getting a good arc. Poor arc length and angle can cause the weld to be weak.
- I’m not keeping the arc consistent. If the arc is too long or too short, it can cause the weld to be weak.
These are some potential causes as to why my stick welds are not holding. If I can identify the cause of the problem, I can adjust my technique and materials to ensure a strong weld.
What type of electrode are you using?
I am using a 7018 stick electrode for my welding. This type of electrode is commonly used for welding thicker metals, which is why it is ideal for stick welding. The 7018 electrode is designed to create a strong, durable weld that will last for years.
However, stick welding can be tricky and there are several reasons why my stick welds may not be holding. The most common cause is improper technique. Stick welding requires an experienced hand and a slow and steady speed. If the electrode is moved too fast, it can cause the weld to be weak and not hold. Additionally, the quality of the electrode and the material being welded can also affect the strength of the weld. Poorly maintained electrodes or electrodes that are incompatible with the material being welded can lead to poor welds.
In order to ensure my stick welds are as strong as possible, I should always make sure I am using the correct type of electrode for the job, that my electrode is in good condition, and that I am welding with the correct technique. Taking the time to ensure these aspects are correct will help ensure my stick welds are strong and durable.
What is the size of the electrodes?
The size of the electrodes depends on the type of metal being welded. Generally, for thin metal, electrodes should be no more than 1/4″ in diameter. For thicker metal, electrodes should be between 3/32″ and 1/8″ in diameter.
If the electrodes are too large, they deliver too much current, leading to a wide, shallow weld. This type of weld may not hold because it does not penetrate deeply enough into the metal. On the other hand, if the electrodes are too small, the current is too low and the weld will be too narrow and shallow.
It is also important to check the electrode angle when welding. If the angle is too shallow, the weld pool will be too shallow and may not hold. If the angle is too steep, the weld pool will be too deep and may cause the metal to crack.
What type of metal are you welding?
I am welding a metal that is difficult to weld. There are a few reasons why my stick welds may not be holding. Here are some of the most common reasons:
- Incorrect current setting – The welding current should be set to the correct amperage for the metal being welded. Too much current can cause the weld to become brittle and fracture.
- Wrong electrode type – The electrode type should match the metal being welded. Incorrectly matched electrodes can cause the weld to be weak and brittle.
- Incorrect joint fit – The joint should be properly prepared before welding. Poor joint fit can cause the weld to be weak and crack.
- Incorrect arc length – The arc length should be kept short and consistent to ensure a strong weld. Too long of an arc length can cause the weld to be weak and crack.
- Incorrect welding technique – The welding technique should be correct for the metal being welded. Poor technique can cause the weld to be weak and crack.
It is important to understand the type of metal being welded and use the appropriate settings and techniques for that type of metal. This will ensure that the weld is strong and will hold.
What is the thickness of the metal?
When it comes to stick welding, the thickness of the metal is an important factor. For stick welding to be successful, the thickness of the metal must meet certain requirements.
Generally speaking, for mild steel, the minimum metal thickness should be 18 gauge (1.2mm) and the maximum should be 1/4 inch (6.4mm). The thickness of the metal will determine the amperage needed for the job, so it is important to get this right. If the metal is too thick, the amperage required will be too high, resulting in poor welds.
The following list outlines some of the common metal thicknesses and the appropriate amperage required for each:
- 18 gauge (1.2mm) – 90-120 amps
- 16 gauge (1.6mm) – 140-180 amps
- 14 gauge (2.0mm) – 180-220 amps
- 12 gauge (2.4mm) – 220-280 amps
- 1/4 inch (6.4mm) – 280-350 amps
In addition to the metal thickness, the type of metal being welded will also affect the success of the weld. Stick welding is not suitable for all metals, so it is important to check that the metal being welded is suitable for stick welding.
If the metal thickness and type are not suitable for stick welding, it is unlikely that the welds will hold. In this situation, it would be necessary to use a different welding process, such as MIG or TIG welding.
Is the welding current, voltage and amperage correct?
It is possible that the welding current, voltage and amperage are not correct, and this could be the reason why your stick welds are not holding. Here are some steps you can take to check if the current, voltage and amperage are correct:
- Check that the welding current is set within the recommended range for the type of material you are welding.
- Check that the voltage is set to the correct level for the type of material you are welding.
- Check the amperage setting to make sure it is within the recommended range for the type of material you are welding.
It is important to ensure that the welding current, voltage and amperage are all correct in order to ensure that the welds hold. If any of these settings are incorrect, it could lead to weak or ineffective welds.
Are you using the correct welding technique?
When it comes to stick welding, there are several key factors to consider to ensure successful welds. It is important to make sure that you are using the correct welding technique in order to achieve a strong weld.
Here are some tips to ensure your stick welds are successful:
- Check the parameters of the welding machine to ensure the correct amperage and voltage.
- Make sure the welding rod is the correct size and type for the material you are welding.
- Ensure the electrodes and material are clean and free of contaminants before welding.
- Keep the electrode at the correct angle, usually between 10 and 15 degrees.
- Use the correct travel speed, usually about 1 to 2 inches per second.
- Make sure the weld joint is the correct size for the material being welded.
By following these techniques, you should be able to achieve a strong and successful weld that will hold. If you are having trouble with your stick welds not holding, it is likely that one of these factors is incorrect.
Are you using the right welding speed?
One of the most common reasons why stick welds may not be holding is due to incorrect welding speed. The welding speed should be adjusted to ensure proper fusion between the two metal pieces. Here are the key points to consider when determining the right welding speed:
- Set the amperage according to the thickness of the metal.
- Set the welding speed between 80 – 120.
- Adjust the speed according to the size and shape of the joint.
- Move the welding rod at a steady speed.
- Allow the welding rod to cool between passes.
Proper welding speed is essential for strong and long lasting welds. If your welds are not holding, make sure to adjust the speed accordingly and practice proper technique.
Is the surface of the metal clean?
One of the main reasons why stick welds may not be holding is if the surface of the metal is not clean. Before starting any welding job, it is important to make sure that the surface of the metal is free from dirt, grease, and other contaminants.
If the surface of the metal is not clean, the weld may not hold due to the following reasons:
- Dirt, grease, and other contaminants can act as an insulator, preventing the weld from properly bonding to the metal.
- Contaminants can cause the molten metal to cool too quickly, resulting in a weak or incomplete weld.
- Contaminants can cause the weld to be porous, resulting in a weak or incomplete weld.
It is important to thoroughly clean the surface of the metal before welding to ensure that the welds will hold. This can be done with a wire brush, sandpaper, or a solvent. It is also important to make sure that the metal is dry before welding to prevent any moisture from affecting the weld.
By taking the time to ensure that the surface of the metal is clean before beginning any welding job, it will help to ensure that stick welds are holding properly.
Are you using the right type of shielding gas?
If your stick welds are not holding, there are several things to consider:
1. Are you using the right type of shielding gas? It is important to choose the right type of shielding gas for the specific welding process you are using. Shielding gases protect the weld from oxygen and nitrogen in the air, which can cause weld defects. For stick welding, a mixture of carbon dioxide and argon gases is typically used.
2. Are you using a suitable electrode? Different types of electrodes are used for different types of metals. For example, an E6010 electrode is used for welding mild steel, while an E7018 electrode is used for welding stainless steel.
3. Are your welds properly prepared? It is essential to prepare your welds correctly. This includes grinding and cleaning the surfaces to be welded and ensuring that the joint has the correct gap.
4. Are you using the right welding technique? It is important to use the correct welding technique for the job. This includes making sure that the arc is correctly positioned and the weld speed is appropriate for the application.
If you are unsure of any of the above, it is recommended to consult an experienced welder or welding expert for advice.