Welding helmets are one of the most important pieces of protective equipment for welders, as they provide a critical layer of safety for the face and eyes. But how are welding helmets rated? Knowing the ratings and standards that welding helmets must meet can help you ensure that you are getting the right level of protection. In this guide, we’ll discuss the ratings systems and standards that welding helmets must adhere to, so you can work with confidence and safety.
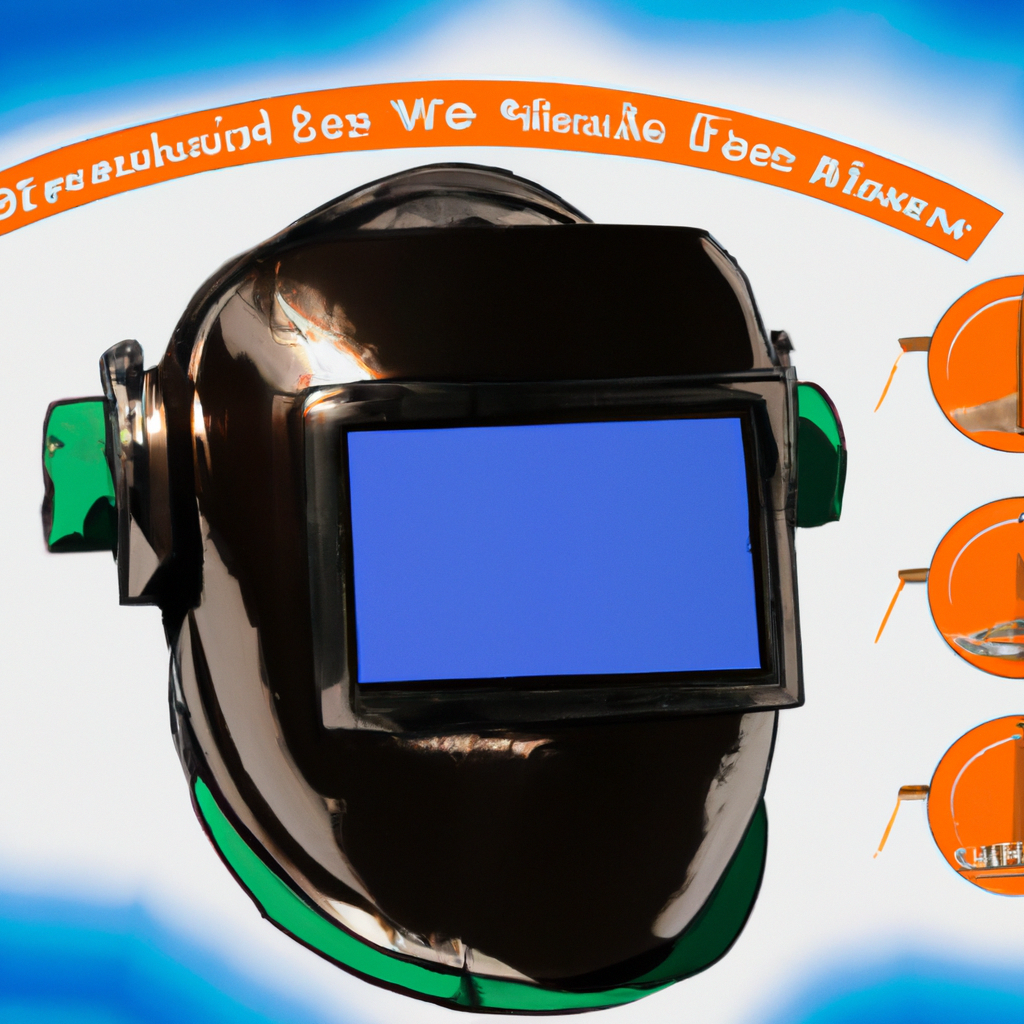
1.What Are Welding Helmets?
Welding helmets are essential safety gear used in welding. They protect welders’ eyes and face from the intense bright light, sparks, and heat created by welding. The helmets also protect welders from harmful radiation like ultraviolet (UV) and infrared (IR) light. Welding helmets are rated according to the amount of light they can block. The ratings range from shade 9, which blocks the least amount of light, to shade 13, which blocks the most. A shade 10 rating is the most common and is suitable for most welding applications.
Welding helmets are also rated for their response time. This is the amount of time it takes for the lens to darken when exposed to the welding arc. The faster the response time, the better the protection. Response times range from 0.10 milliseconds (ms) to 0.50 ms and are often marked on the helmet. It is important to choose a welding helmet with the correct shade and response time for the application.
2.What Standards Are Used to Rate Welding Helmets?
Welding helmets are typically rated according to two standards: ANSI Z87.1 and EN379. ANSI Z87.1 is the American National Standards Institute’s standard for the protection of eyes and face. It sets forth requirements for the design, manufacture, performance, testing and labeling of eye and face protection products used in the workplace. The EN379 standard is the European standard for eye and face protection and sets requirements for the design, manufacture, performance, testing and labeling of welding helmets and their components.
The ANSI Z87.1 standard rates welding helmets according to their ability to protect the user’s eyes from the intense light emitted by the welding process. This rating is based on the amount of light the helmet allows to pass through it, with higher ratings indicating that the helmet is more effective at blocking out light. Helmets are rated from 0 to 1, with 1 being the highest level of protection.
The EN379 standard is slightly different and rates welding helmets according to their ability to protect the user’s face from the intense heat generated by the welding process. Helmets are rated from 0 to 4, with 4 being the highest level of protection. The ratings are based on the amount of heat the helmet is able to absorb, with higher ratings indicating that the helmet is more effective at blocking out heat.
3.What Are the Different Types of Welding Helmet Ratings?
Welding helmets are rated according to their optical clarity, shade range, and sensitivity. The optical clarity rating is determined by how well the helmet protects the welder’s eyes from the intense light emitted from the welding arc. The shade range rating is determined by how dark the shade of the helmet’s lens is and the sensitivity rating is determined by how quickly the helmet can darken when exposed to the bright light generated by welding.
The ratings are usually categorised into four categories:
- Shade 1-4, which is the lowest level of protection and is suitable for use during light-duty welding tasks.
- Shade 5-9, which offers a greater level of protection and is suitable for medium-duty welding tasks.
- Shade 10-13, which is the highest level of protection and is suitable for heavy-duty welding tasks.
- Shade 14-16, which offers an even greater level of protection and is suitable for the most extreme welding tasks.
When selecting a welding helmet, it is important to select one with a rating that is appropriate for the type of welding being performed. It is also important to select a helmet with a good optical clarity rating, as this will help to ensure that the welder is able to clearly see the welding arc.
4.What Are the Advantages of Having a Rated Welding Helmet?
Welding helmets are rated for their ability to protect a welder from the intense light and heat generated by the welding process. The rating of a welding helmet is based on the level of protection it provides against ultraviolet (UV) and infrared (IR) radiation, as well as its ability to block sparks and spatter. Here are the advantages of having a rated welding helmet:
- A rated welding helmet offers maximum protection against the intense light and heat generated by the welding process.
- It protects the welder from the harmful UV and IR radiation emitted by the welding arc.
- It is designed to block sparks and spatter from reaching the welder’s eyes and skin.
- It provides a better and more comfortable fit than an unrated welding helmet.
- It helps to reduce the risk of eye strain and fatigue caused by the intense light and heat of the welding process.
5.What Is the Difference Between ANSI and CE Ratings?
ANSI and CE ratings are two standards for rating the welding helmets. ANSI stands for American National Standards Institute, which is a non-profit organization that sets standards for safety and performance in the United States. CE stands for Conformité Européenne, which is a European standard for safety and performance.
The main difference between ANSI and CE ratings is that ANSI ratings are based on the United States standards, while CE ratings are based on European standards. ANSI ratings are more stringent and require a higher level of protection, such as full-face coverage and more reliable eye protection. CE ratings are more flexible and allow for more variations in protection, such as half-face coverage and less reliable eye protection.
When it comes to welding helmets, ANSI ratings are based on the American Welding Society’s standard, which includes rigorous testing of the helmet’s eye protection and impact resistance. CE ratings are based on the European Union’s standard, which also includes testing of the helmet’s eye protection and impact resistance, but with less stringent requirements than ANSI.
In conclusion, the main difference between ANSI and CE ratings is that ANSI ratings are based on the United States standards, while CE ratings are based on European standards. ANSI ratings are more stringent and require a higher level of protection, while CE ratings are more flexible and allow for more variations in protection.
6.What Are the Different Categories of Welding Helmets?
Welding helmets are rated based on their ability to protect the welder from the intense light, heat, and radiation generated by welding. The categories of welding helmets are:
- Shade Ratings: Shade ratings indicate the amount of light that is blocked by the helmet and are measured on a scale of 9-13. The higher the number, the more light is blocked.
- Lens Speed: Lens speed refers to the amount of time it takes for the lens to darken after it is exposed to the arc. The faster the lens speed, the better the protection.
- Sensitivity Settings: Sensitivity settings refer to how quickly the lens reacts to the welding arc. The higher the sensitivity setting, the more quickly the lens will darken.
- Viewing Area: The viewing area is the amount of space that the welder can see through the helmet and is usually measured in square inches.
- Auto-Darkening Feature: An auto-darkening feature automatically darkens the lens when the welding arc is detected, providing the welder with improved visibility and protection.
Each welding helmet also comes with a user-friendly control panel that allows the welder to adjust the settings according to their needs and to ensure that they have the best possible protection.
7.What Are the Different Levels of Protection Offered by Welding Helmets?
Welding helmets are rated according to the levels of protection they provide. Generally, helmets are rated based on their ability to protect the wearer from the intense light and heat generated by welding processes. The most common levels of protection include:
- Shade 9 – This level of protection offers the least amount of shielding, and is typically used for torch brazing applications.
- Shade 10-12 – These levels of protection are suitable for light welding applications, such as MIG welding.
- Shade 13-14 – These levels of protection are ideal for more intense welding processes, such as TIG welding.
- Shade 15 – This level of protection offers the highest level of shielding, and is typically used for welding processes that involve higher levels of heat, such as plasma and laser welding.
The levels of protection offered by welding helmets can also be affected by the type of lens used. For instance, some helmets use a flip lens that can be quickly switched between different shades, while others use a fixed lens that is permanently set to a specific shade.
8.What Is the Best Rated Welding Helmet for Your Needs?
The best rated welding helmets are determined by a variety of factors, including features, protective capability, and overall value. Here are a few of the most highly rated welding helmets on the market:
- Antra AH6-260-0000 Solar Power Auto Darkening Welding Helmet: This helmet offers a 1/1/1/1 optical clarity rating, a 3.86” x 1.73” viewing area, and a delay control feature.
- Jackson Safety W70 BH3 Auto Darkening Welding Helmet: This welding helmet is well-known for its reliability, comfort, and superior clarity ratings.
- Miller Electric Digital Elite Auto-Darkening Welding Helmet: This welding helmet offers a large viewing area, an adjustable headgear, and a grind mode.
In addition to the features, welding helmets are also rated based on the level of protection they offer. The American National Standards Institute (ANSI) has set safety standards that all welding helmets must meet. Helmets are rated on a five-scale system from 1 to 5, with 5 being the highest level of protection.
9.How Can You Ensure a Safe Welding Process With Your Rated Helmet?
To ensure a safe welding process with a rated helmet, there are a few important steps to take. These include:
- Check to ensure the helmet meets the safety requirements of American National Standards Institute (ANSI) and Occupational Safety and Health Administration (OSHA) standards.
- Ensure the helmet fits properly and is the correct size for your head.
- Check the helmet to make sure it is in good condition and free of damage.
- Always use the proper lens shade for the type of welding you are doing.
- Regularly check the helmet for wear and tear, and replace it if necessary.
- Ensure the helmet has adequate ventilation to prevent heat buildup.
- Never leave a welding helmet unattended while it is in use.
By following these safety steps, you can ensure that your welding helmet is rated correctly and that you are working in a safe environment.
What are the Best Methods for Preventing Welding Helmet Fogging?
To stop welding helmet fogging instantly, there are a few effective methods. One is to use anti-fog coatings or sprays that can be applied to the helmet’s lens. Additionally, ensuring proper ventilation in the workplace can help minimize fogging. Another solution is to opt for helmets with built-in fans or air vents, promoting airflow and reducing moisture buildup. Finally, regularly cleaning and drying the helmet’s lens can prevent fogging during welding processes.
What Are the Benefits of Using a Rated Welding Helmet?
A rated welding helmet is designed to protect the face and eyes of the welder from sparks, heat, and ultraviolet and infrared radiation. It also helps to reduce the risk of eye and skin damage caused by these elements. The rating of the welding helmet determines the amount of protection it provides.
The benefits of using a rated welding helmet include:
- Increased protection from welding sparks, heat, and radiation
- Reduced risk of eye and skin damage
- Comfort and stability while welding
- Improved visibility and control
- Reduced fatigue from working long hours
How are welding helmets rated? Welding helmets are typically rated according to the amount of protection they provide from ultraviolet and infrared radiation. The higher the rating, the better the protection. The American National Standards Institute (ANSI) is the most commonly used rating system for welding helmets.