Using an electric welder can be a daunting task, but with a few simple steps and some practice, you can be an expert welder in no time. An electric welder is a powerful tool, capable of joining metal pieces with ease and precision. Whether you are welding for a hobby or for a profession, the right weld can make the difference between a strong joint and a weak one. With the right knowledge and guidance, you can quickly master the art of welding and make sure your projects last for years to come.
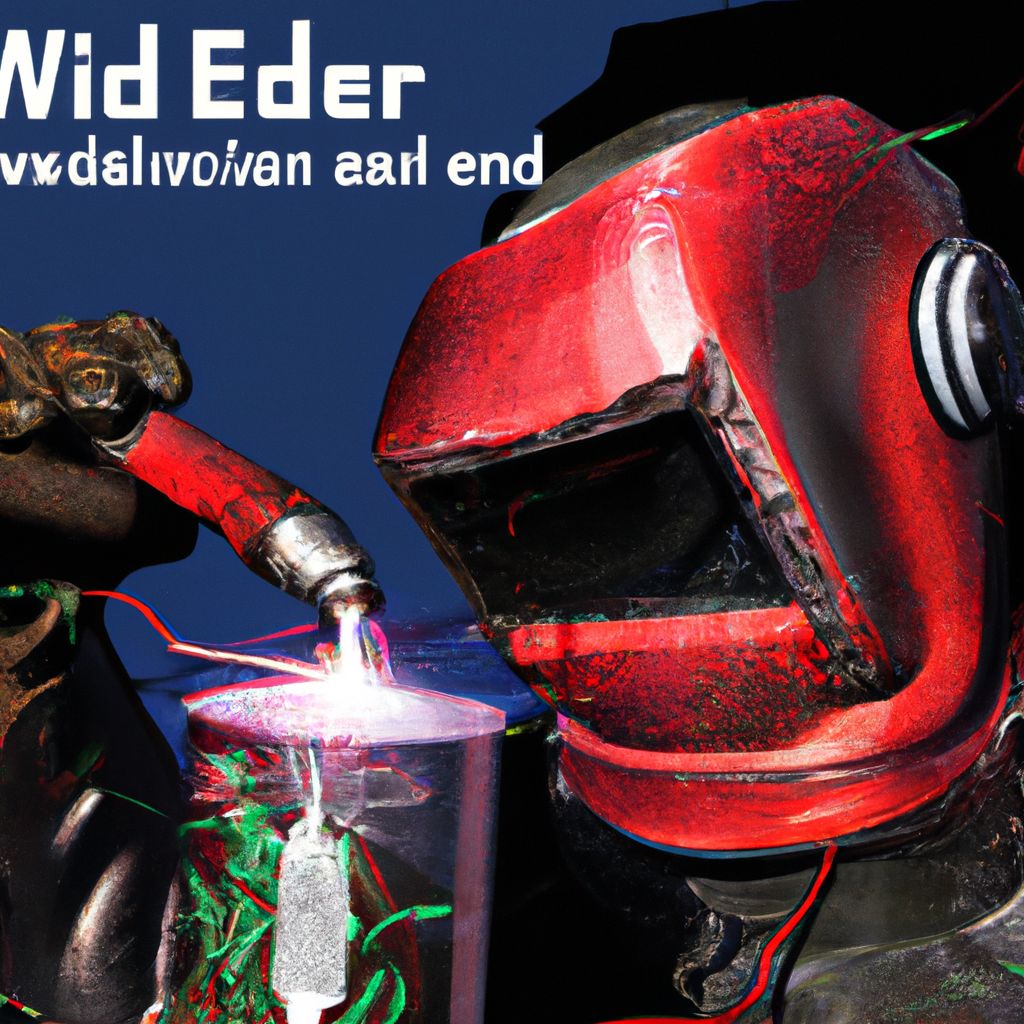
What Safety Precautions Should be Taken Before Using an Electric Welder?
When using an electric welder, it is important to take the proper safety precautions. Here are some of the key safety tips to follow when using an electric welder:
- Wear appropriate clothing, including leather boots, a welding helmet, protective gloves, and a long-sleeve shirt made of natural fibers.
- Make sure the welding area is free of any combustible materials or debris.
- Ensure that the welding machine and all related materials are properly grounded.
- Ensure the area is well ventilated.
- Always use the correct welding rod for the job.
- Check the power and welding cables regularly for any damage.
It is also important to keep your workspace clean and organized. Make sure that all tools and materials are properly stored and that the welding area is free of any flammable materials or debris. Additionally, it is important to be aware of your surroundings and the potential hazards that may be present.
Finally, always make sure that the electric welder is properly set up and that the safety features are engaged. Never leave the machine running unattended and always turn it off after use. By following these safety precautions, you can ensure that your welding experience is safe and productive.
What Type of Electric Welder Should I Use?
Using an electric welder can be a great way to complete a variety of projects. However, the type of welder you use depends on the project you are doing and the materials you are working with. Here are a few tips for choosing the right electric welder for your project:
- For projects involving thin metals, such as sheet metal, a MIG welder is the best option.
- For thicker metals, such as steel, a TIG welder is the best choice.
- For projects involving aluminum, a stick welder is recommended.
- For projects involving stainless steel, a flux-cored arc welder is the best option.
When selecting an electric welder, be sure to consider the power output. For most projects, an electric welder with an output of around 80 amps is sufficient. However, for heavier-duty projects, you may need a welder with an output of up to 120 amps.
Once you have chosen the right electric welder for your project, it’s important to read the instructions for use carefully. Following the instructions will help ensure that you use the welder safely and get the best results.
How Do I Connect the Electric Welder to a Power Source?
To connect an electric welder to a power source, you will need to follow these steps:
- Make sure the power source is compatible with the welder. Check the voltage rating and current rating of the power source and compare it to what is recommended for the welder.
- Verify that the power source is turned off and unplugged before you connect the welder.
- Connect the power cables of the electric welder to the power source. Check to make sure that the connections are secure.
- Plug the power source into an outlet and turn it on.
- Switch the power switch of the welder to the “on” position.
- Adjust the current output to the desired level. For most welding applications, the output should be around 80 (maximum 120).
Once the welder is connected to the power source and the settings are adjusted, you are ready to begin welding.
What Types of Welding Rods Should I Use?
When using an electric welder, the type of welding rod you use will depend on the type of material you are working with. Here are some common types of welding rods and what they are used for:
- Mild steel: These rods are used for welding low-carbon steel and are available in a variety of sizes and shapes.
- Stainless steel: These rods are used for welding stainless steel and other alloys. They are available in a variety of sizes and shapes.
- Aluminum: These rods are designed for welding aluminum and other non-ferrous metals. They come in various sizes and shapes.
- Cast iron: These rods are designed for welding cast iron and other ferrous metals. They come in a variety of sizes and shapes.
When selecting a welding rod, you should always consider the thickness of the material you are working with, as well as the type of joint you will be making. This will help you select the right rod for the job.
How Do I Set Up the Electric Welder?
Setting up an electric welder is a relatively straightforward process. Here are the steps to follow:
- Put on your safety gear, including a welding helmet, gloves, and apron.
- Connect the power cord to the wall outlet and set the amperage to the desired setting.
- Connect the welding cable to the welder and the work piece.
- Adjust the gas pressure and flow according to the material being welded.
- Set the welding current to the desired output, usually around 80-120 amps.
- Strike an arc by holding the electrode to the workpiece and pulling the trigger.
Once the arc is established, you are ready to begin welding. Be sure to maintain a consistent arc length and keep the electrode moving at a steady pace. With practice, you will become a proficient welder.
What Technique Should I Use When Operating the Electric Welder?
When operating an electric welder, it is important to take safety precautions and follow certain procedures. Here are a few tips to help you get the most out of your electric welder:
- Wear protective clothing to protect against sparks and spatter.
- Make sure the area is well ventilated to avoid fumes.
- Check all connections and cords to ensure they are secure and there is no damage.
- Select the correct welding rod for the material you are working with.
Now you are ready to begin welding. Set the amperage and voltage to the recommended settings for the material you are welding. Connect the welding electrode to the power source. Strike an arc and adjust the arc length to the desired amount. Move the electrode along the joint, maintaining a constant arc. To ensure penetration, maintain a steady speed along the joint.
When you are finished welding, turn off the power source and disconnect the welding electrode. Make sure to clean up any spatter or debris that accumulated during the welding process. Finally, inspect your work and make sure it is up to code.
By following these simple steps, you will be able to operate your electric welder safely and effectively. With practice, you will become more efficient in your welding processes.
How Do I Know When the Weld is Completed?
When you are welding with an electric welder, it is important to know when the weld is completed. Here are a few tips to help you identify when the weld is done:
- Check for a strong weld joint. If it is weak, it is likely not complete.
- Look for a good amount of sparks and smoke. This indicates that the weld is heating up properly.
- Listen for a loud snapping sound that indicates the metal pieces are joining together.
- If the weld is done correctly, you should see a nice, glossy finish on the welded area.
When the weld is complete, the output should be around 80. If it is higher than 120, the weld may be too hot. It is important to practice using your welder so that you can get a good feel for when the weld is complete.
Are There Different Techniques for Different Types of Welds?
Yes, there are different techniques for different types of welds. To use an electric welder, the following steps should be taken:
- Select the appropriate type of welding process for the job. This includes selecting the type of current, voltage, wire size, and welding speed.
- Ensure that the welding area is clear of debris and that the surfaces to be joined are clean and free of contaminants.
- Connect the welding machine to the power source.
- Adjust the amperage and voltage settings according to the type of weld being performed.
- Place the welding wire into the weld puddle.
- Move the welding gun in a circular motion to ensure the weld is even.
- Use a chipping hammer and wire brush to remove any slag from the weld.
- Inspect the weld for any defects.
With the right technique, electric welders can be used effectively to create strong and durable welds.
What Maintenance is Necessary After Using an Electric Welder?
Once you have finished using your electric welder, it is important to take the necessary steps to ensure that it remains in good condition for future use. Here are some tips for maintaining your electric welder:
- Make sure to switch off the power to the welder after use and unplug it from the wall.
- If the welding torch was used, ensure that it is disconnected from the welding machine.
- Use a cloth or rag to clean the welding machine and the welding torch.
- Check the cables and leads for any signs of damage or wear and tear. Replace any cables or leads that are damaged.
- Check the torch for any signs of wear or damage. If necessary, replace the torch tip or other parts.
- Check the contact tip for any signs of wear or damage. Replace the contact tip if necessary.
- Check the ground clamp for any signs of wear or damage. Replace the ground clamp if necessary.
- Check the welding machine for any signs of wear or damage. Replace the welding machine if necessary.
- Check the welding wire for any signs of wear or damage. Replace the welding wire if necessary.
- Check the gas hose for any signs of wear or damage. Replace the gas hose if necessary.
By taking the time to properly maintain your electric welder, you can ensure that it will provide years of reliable service.
How Can I Ensure the Quality of My Welds?
There are a few key steps to ensure the quality of your welds when using electric welding:
- Always wear safety equipment, such as gloves, a face shield, and long pants and sleeves.
- Read the manufacturer’s instruction manual for the welder to understand the machine’s capabilities and limitations.
- Use the right welding rod for the job.
- Set the welding current to the correct amperage.
- Clean the surface that you are welding.
- Maintain a steady and consistent welding speed.
- Check the weld for any imperfections.
Following these steps can help ensure that your welds are of high quality. Working with an experienced welder is also a great way to get tips and advice on the welding process.