Becoming a skilled welder is as much about training as it is about talent. A proper weld is more than just an understanding of how to properly apply the right amount of flame and filler rod to the base metal. It is an art. It takes skill and talent, a steady hand, and a lot of know-how to be able to become a skilled welder.
To ensure that welders are able to properly perform the task at hand, there are tests that have been developed that allow one to determine the skill of the welding operator. This will let you know if you can depend on the quality of the weld and the strength of the joint that has been welded. These tests help to find any defects that may not be visible simply by looking at them.
Destructive Tests
This test is exactly as its name would imply. It is looking to determine when the weld will give way, and includes tensile and betting tests. In this type of experiment, the specimens are loaded and tell they give way. This gives the tester the information needed to ascertain the quality of the weld.
Destructive tests come in two types: workshop and laboratory. There are also non-destructive tests (NDT). These include using such things as x-rays and hydrostatic tests that do not destroy or damage the weld in any way as the name implies, the goal of this type of test is to determine the strength of the weld without causing any physical damage.
Acid Etch Test
What you will find is that most welds are tested using destructive tests. This is why we will spend much of the next several sections discussing the different types of destructive tests. The first of these is the acid etch test.
In this type of test the weld itself is tested to determine the soundness of that weld. Acid is added, which reacts with the edges of the cracks in the base or weld metal. This instantly discloses weld defects if they are present. If they are present, it also accentuates any boundaries there are between the base and weld metal.
Acids such as hydrochloric and nitric, ammonium persulfate, and iodine or potassium iodide are commonly used for etching low alloy or carbon steels. The test is performed on a cross-section of the joint.
Guided Bend Test
One of the most important parts to test regarding any weld is at the face and root of the welded joint as well as determining the degree of penetration and fusion that have occurred with the base metal. This is best accomplished using the guided Bend test.
This test is designed to provide an accurate assessment of the efficiency of the weld. The test specimens are machined from the materials that were welded together. The thickness of this material has to be within the capacity of the bending jig.
To properly tested, the specimen is placed across supports. A plunger, which is a hydraulic jack or other similar device, is used by the operator to punch at the material. If successful, it should force the test specimen into the jig, taking on the shape. A properly tested and approved specimen will band 180°. This meets the standards as possible, but there cannot be any cracks greater than 1/8 of an inch.
Free Bend Test
The free bend test is just about how it sounds. This test is designed to measure how easy it is to bend a welded material. This is often referred to as ductility. To perform this type of test a specimen is machined from the welded plate. Each corner of the specimen is then rounded and a radius to not exceed 1/10 of the overall thickness of the specimen. Then, to scribed lines are drawn on the face about 1/16 of an inch from the edge. The distance from each of these lines is then measured in inches and recorded.
The next step is to actually test the specimen. It is placed in the device that attempts to bend it to angles of about 30°. A proper positioning of the testing material is performed prior to the test to ensure that only the weld and its ductility are being tested.
Once the specimen is initially bent and successfully passes the test, or force is applied to the specimen to see if it can be bad further. If a crack forms the 16th and in any place, then the weld is considered to be a failure. Bending is continued until it has passed all subsequent tests or it has reached a state of failure.
Once the test is concluded, a material meets the standards as passable when the distance between the lines drawn on the specimen meet the mathematical equation that fits the standard. There can be no cracks greater than 1/16 inch.
One important note. When using a vise or other similar type of compression device to perform the test, it is important to ensure that the upper and lower contact plates are parallel to the ends of the specimen. This ensures that there will be no slipping or snapping while the test is being performed.
Back Bend Test
This test is used for two purposes, to test the quality of the weld metal and also to test the degree of penetration into the weld. This is usually testing the penetration to the Y of the welded butt joint.
The specimens that are used are basically the same ones that are used for the free bend test with the exception that they are bent at the root of the weld. Those specimens that are tested are bent 90°, to ensure that they do not break apart. While this test has been a popular choice in the past, it has basically been replaced by the guided bend test.
Nick Break Test
The purpose of this test is to determine if there are any internal defects in the welded butt joint in the metals that have been welded together. These defects can include such things as gas pockets, poor fusion, sly conclusions, or oxidized or burnt metal.
To perform this test, a specimen is selected from the welded butt joint. This is acquired by machining or by cutting a piece with the oxyacetylene torch. To obtain the specimen, each edge of the weld at the joint is to be slotted using a saw cut through the center. This piece is then bridged across to steal blocks and is struck using a heavy-duty hammer. This is done and tell the weld begins to fracture.
Once the fracture occurs, the welder is able to examine the exposed area to ensure that the metals were fused together completely and that they are free from any slack conclusions. There must not be any gas pocket greater than 1/16 inch and there is a limit to the number of gas pockets that can be present per square inch. This is to be no more than six.
While this is the most common method used in the break test, another means that can be used is to employ force by using a press or testing machine. This delivers blows much like that of a hammer against the welded fillet. Again, once a fracture is created it is examined to check for the soundness of the weld.
Tensile Strength Test
This type of weld is specifically designed to measure the strength of the joint that is welded. To determine the strength, a portion of the weld plate is checked. The portion reviewed is where the plates combine about midway between the jaws of the testing machine. During the test, the width thickness is measured to begin, looking for an area and square inches that is calculated. This area is then multiplied by two figures, the width of the weld itself, and the measurement of the plates involved.
The test specimen is then mounted in a machine that exerts enough pull on the piece to be able to break the specimen apart. While many use stationary machines, there are also portable types that are quite good. The portable type uses a hydraulic principal and is capable of pulling as well as bending the test specimen. This allows for two types of measurements to be taken.
As the specimen is being tested, the load in pounds is registered on the gauge. It is specifically the load at the point where the weld breaks that is recorded. This value is then measured by multiplying the width of the weld times the tensile load. That value is then divided by the area to give a proper tensile strength. This measures in pounds per square inch.
When measuring the strength of traverse and longitudinal fillet welds, the measurements began by measuring the width of the specimen in inches. The specimen is then ruptured under the tensile load that is applied. This gives the maximum load in pounds. The sharing strength is then measured in pounds per linear inch and is determined by the maximum load divided by the length in inches. Sharing strength is measured in pounds per square inch and is determined by the sharing strength divided by the area in square inches.
Non-Destructive Tests
There are several different non-destructive tests that can be performed.Hydrostatic Test
This is the first of these tests, and is used to check the quality of the weld on closed containers, such as those like pressure vessels and tanks. To properly test the weld, the vessel is filled with water applying a great deal of pressure to the container. Additional pressure can be applied beyond the water volume itself. This test can also be performed using oil and steam. If any seepage is noted during the test, then the amount of pressure being applied at that point is recorded.
Magnetic Particle Test
This type of test is made on parts using magnetic alloy steels. Specifically, the test only works with ferromagnetic materials in which the deposited weld is also made of a ferromagnetic material. To test this type of weld, a strong magnetic field is created using a high amperage electric current. The magnetic field is increased in current, and a leakage field is tested. The current level is checked once the leakage is created.
X-Ray Testing
The x-ray testing method is exactly how it sounds. Using a radiographic x-ray tube machine, areas around the weld are x-rayed to check for any cracks, blowholes, slagged, or other zones where a proper fusion has not been created. Defective spots show as dark spots and bands.
When using this type of testing method, it is important that the person performing the test use the proper procedures to protect themselves. X-rays can be dangerous, and this is why it is necessary that a person follow the American Standard Code for the Industrial Use of X-rays.
Gamma Ray Test
This kind of test is similar to the x-ray method, but differs in that it uses gamma rays to test the weld. In this type of test, instead of using an x-ray tube, a capsule of radium sulfate is used. This creates shorter wavelengths, which determines when it is applicable. In welds that are thicker, it takes a considerable amount of time for the gamma rays to work their way through the weld, which may be a factor in using the test. If time is not a factor, this is one method that is considered to be one of the best because of the deep penetration and amount of revelation it supplies.
Florescent Penetrant Test
This type of test uses special dyes that reveal cracks, leaks, pores, or other problem areas that could create problems within the weld. There are different types of dyes that are used for specific materials, allowing you to test welds for magnesium, aluminum, or other types of metals and steels. This is a great way to perform a test, as you simply need to rinse away the dye once the test is concluded.
The dyes reveal cracks, leaks, and other blemishes by seeping into these areas and presenting a fluorescent color that is visible. Once the test is concluded, all you have to do is rinse, spray, or brush the area and the die is removed. Of course, if there is an issue with the weld, that it is important to fix the weld and test once again.
There are a number of advantages in using this type of procedure, most importantly related to cost. These dyes are relatively inexpensive, especially considering that no damage is caused to the weld itself. It also is great for use in both ferrous and non-ferrous metals.
However, the capability of this weld is quite limited. Crack or pour may have developed underneath the weld, something that would be inaccessible to the dye itself. This means that a potential problem may not be visible to you.
Which Welding Electrodes are Suitable for Different Types of Weld Testing?
When it comes to different types of weld testing, using the right welding electrodes is crucial. The welding electrode selection guide helps in determining the suitable electrodes for each test. This ensures accurate and reliable results, whether it’s for destructive or non-destructive testing methods. Proper electrode selection enhances weld quality and contributes to successful test outcomes.
Hardness Tests
Beyond the non-destructive tests, there are a series of hardness test that can be conducted as well. These tests are testing to ensure how resistant the material is to indentation. What that means is that pressure is applied to the weld to see if a dent or other type of indentation can be created. It is the amount of pressure applied that provides the answer to the quality of the weld created. There are several different types of hardness tests that can be performed.
File Test
This is the simplest method that can be used. This type of test is determining the comparative hardness of the material and is conducted by running a file across the weld using manual pressure. This allows you to see if there are areas where it is harder or softer.
Hardness Test Machines
There are also machines that can be used to test the level of hardness. Each of these test is designed to provide a specific type of function. While you can use more than one machine on a welded area, it is important to understand that no single machine is able to perform all tests related to hardness.
Brinell Hardness Tester
This machine uses a mathematical formula to determine level of hardness using the Brinell machine, the specimen is mounted on the anvil of the machine and a pressure load of 6620 pounds is applied against the material using a hardened steel ball. The pressure is applied for 30 seconds and is then released. The diameter of the depression is then measured. This is important to note. The test is not measured the depth of the depression, but is measuring the diameter itself. This test then uses the following formula to determine the hardness of the weld.
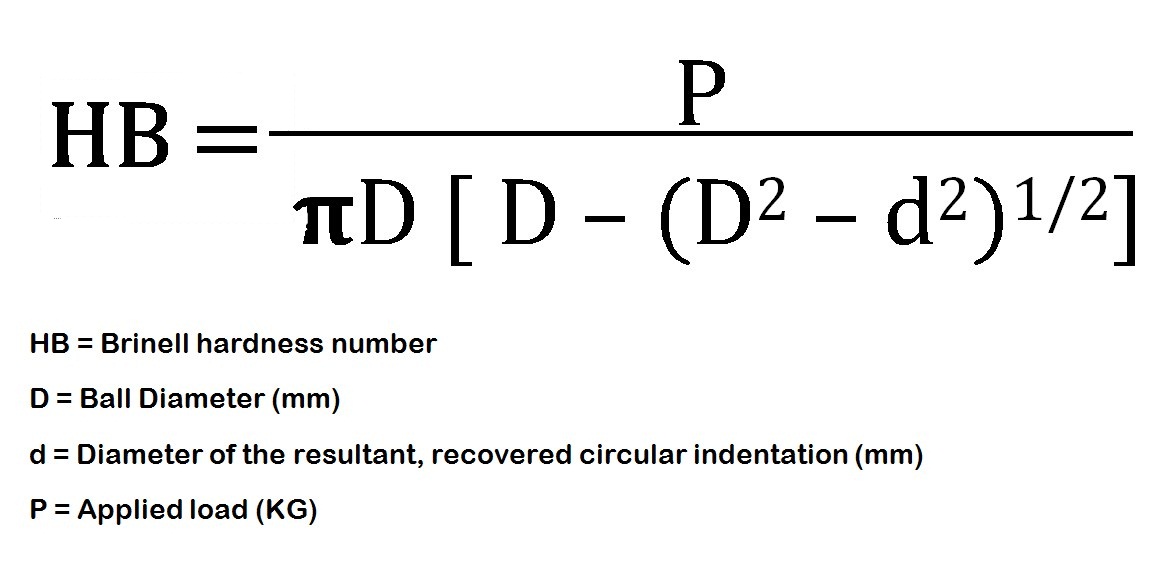
Rockwell Hardness Test
This test operates very similar to the Brinell, but instead of using a small ball, it is most often that a cone shaped diamond is applied. This test is specifically determining the depression of the indentation.
Magnaflux Test
This is another type of non-destructive physical weld test, but it is performed quickly. This test is specifically looking to locate defects that are near the surface of the steel and is performed by using magnetization and ferromagnetic particles.
The way this test works is actually pretty simple. Ferromagnetic powders are dispersed across the weld area. A magnetic field is then created to see if these particles can be moved into the welding area. If they are able to move into cracks, leaks, or other areas of the weld, then an issue has been discovered. The advantage of this type of test is that even if the crack is underneath the surface, it still may reveal that there is an issue by the movement of the ferromagnetic particles.
Acoustic Emission Testing
While this type of test is still commonly used by many welders, it is not considered to be one that should be the primary choice. The reason behind this is that it is difficult for an inexperienced welder to be able to test the acoustics of the weld and find issues. Only welders who have been using this kind of test for years are able to properly perform it. It is as much an art as a skill, and this is why other methods should be used before employing this test.
Ferrite Testing
There is one more task we would like to tell you about. In austenitic stainless steel weld deposits, there is a tendency for small phasers to develop. These fissures tend to be located transverse to the weld fusion line where the weld passes the base metal. This frequently happens when this area has been reheated to near that of the melting point. As a result, cracks appear, which can lead to serious issues related to the tolerance.
The ferrite test looks to find if there are any of these cracks that have appeared. This test can be quite accurate and has been great at finding larger size cracks. However, like the acoustic emissions test, it requires a person who is a skilled welder to be able to perform it properly.
No doubt that this has been a lot of information about how you can test a weld. If you are a welder who works at specific materials, you may never use some of these options, but it is good to know about. You never know if you were going to be in a situation where you will be testing materials that are unfamiliar to you, and it is good to know that you have a good starting place on performing a proper test.