Welding electrodes are one of the most important elements of the welding process. These are metal wires that are coated, and are made out of the same material of that of the metal pieces which are being welded together.
While the composition of the metal piece is obviously the most factor related to the welding electrode, it is not the only factor. Other factors are important in choosing the right electrode, and this guide will not only give you information that you need to know to help you to choose the right electrode, but will also give you information on sizes, and uses for electrodes.The Consumable Electrode
Before advancing must further into this article, it is important to consider one of the most important factors of the electrode – if it is consumable. What this means is if the electrode melts during the welding process so that it actually becomes part of the weld itself. Certain types of welding processes require consumable electrodes to perform the weld. Others require a non-consumable electrode. In these cases, a welding rod is required. TIG electrodes are one electrode that is non-consumable.Keeping Other Factors in Mind
There are two other factors that need to be considered before diving deeper into this guide. Cleanup is one significant factor. When you are using a consumable electrode, it is blending into the weld itself. That means that there could be beating, spatter, or other debris that could be difficult to clean. Some of these provide a very small amount of spatter, so cleanup is quite easy. However, one thing that many welders have learned is that there are certain types of welding techniques that will create a larger degree of spatter than others. There were also some types of electrodes where this will occur. These are factors that must be considered when determining the kind of electrode you want to use and the kind of welding process you want to employ. You also want to find the right electrode for storage. Consider the fact that some need to be stored in a moisture-free environment, which not only means that there can be no humidity, but that you also have to be careful when removing them from the package. Moisture on your fingers may damage the other electrodes in the package. Thus, your choice may be dependent upon your capability for storage and handling.Electrode Classifications
Understanding the different electrode identification systems for arc welding is important in this industry. The classification number system for these welding electrodes has been universally adopted by the welding industry, and understanding the difference between each is essential to making the right kind of weld. It is also essential in ensuring that the proper tools are being used to create the weld. E – this classification indicates that the electrode is used for arc welding. First 2 or 3 digits – the first two or three digits listed in the classification indicate the tensile strength in thousands of pounds per square inch for the metal that is deposited. The tensile strength is classified as the resistance of the material to forces trying to pull it apart. Third or fourth digits – this number depends upon whether there are two or three digits initially used to describe the tensile strength. This next number indicates the position of the weld. For example, zero indicates that a classification is not used. One tells the welder that it can be used in all positions. Two is for flat and horizontal positions only. Three tells the welder that it must be used for flat positions only. The fourth or fifth digit – this number indicates the type of electrode coating and the type of power supply that must be used. This would mean that either alternating or direct-current and either straight or reverse polarity can be used. The type of coating is the next classification. A description of these factors is indicated in the table listed below.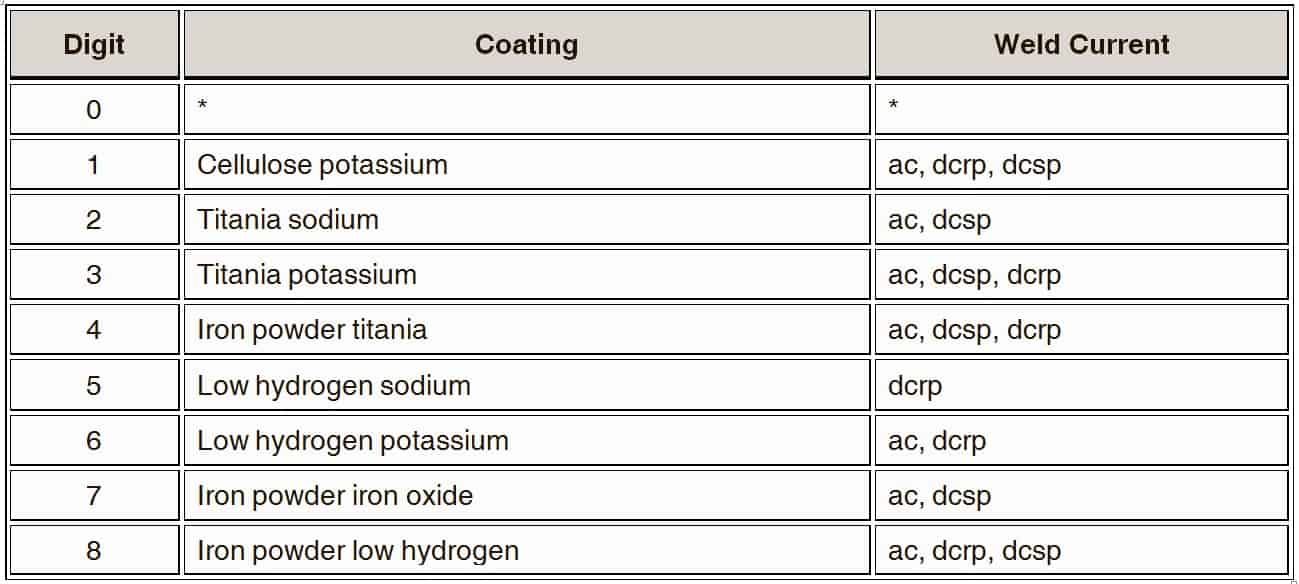
Important Information about Submerged Arc Electrodes
We will not get too deeply into the classification system regarding submerged arc electrodes, but there are some points that we feel are necessary to make. It starts with the initial two letters. As with the other classification, E is the first letter that is listed, and is followed by either an L, M, or H. This indicates the level of manganese that is included. In submerged arc welding, the American welding Society has provided a specific type of classification focused on “bare mild steel electrodes and fluxes for submerged arc welding.” This classification provides both the wire composition and the weld deposit chemistry based upon the type of flux that is used. For filler reds used in oxyfuel gas welding, the prefix R is followed by a G. This indicates that the rod is only to be used for gas welding. The letters are then followed by one of the three 2-digit combinations, either 45, 60, or 65. These indicate the tensile strength in 1000 psi. When non-ferrous filler metals are used, the prefix of E, R, or RB our used. This is then followed by the chemical symbol of the principal metals used within the wire. The most important factor in solid welding electrode wires and rods is the composition. The specification provides the limits of the composition for each wire as well as mechanical property requirements.Electrode Coatings
You will find that the coatings used for welding electrodes that are used in mild and low alloy steels will have anywhere from 6 to 12 different ingredients included. These include:- Cellulose
- clays and goblins
- calcium fluoride
- metal carbonates
- alloying metals, including such things as chromium, nickel, and molybdenum
- mineral silicates
- Ferromanganese
- titanium dioxide
- iron or manganese oxide
- iron powder
- Cellulose-sodium (EXX10): this kind of electrode uses a cellulose material made out of wood flour and could have as much is 30% paper included in the electrode.
- Cellulose-potassium (EXX11): this electrode is quite similar, except for the fact that potassium is used in the place of sodium.
- Rutile-sodium (EXX12): in this type of electrode, there is a higher amount of rutile or titanium dioxide in comparison to other components. This type of electrode is usually quite appealing to the welder because of the quality of the weld and arc that is produced.
- Rutile-potassium (EXX13): this is very similar to the previously listed electrode with the difference being that potassium is used to create the arc ionization.
- Rutile-iron powder (EXX14): very similar to the two previous examples, but 25 to 40% of the electrode is made with iron powder.
- Low hydrogen-sodium (EXX15): this kind of electrode contains a coating that has a high proportion of either calcium carbonate or calcium fluoride.
- Low hydrogen-potassium (EXX16): this type of coding is similar to the previous example, except for that potassium is substituted for sodium.
- Iron oxide-sodium (EXX20): this contains a high amount of iron oxide, which produces a large amount of slagged during the welding deposit.
What Welding Code Should I Use When Selecting Electrodes?
When selecting electrodes for welding, it’s important to understand the common welding codes associated with the process. These codes serve as industry standards and guidelines, ensuring safe and reliable welds. By familiarizing yourself with the specific code applicable to your project, you can confidently choose the appropriate electrodes for the job.
Types of Electrodes
Finally, we want to end by describing the different types of electrodes to you.Bare Electrodes
Bare welding electrodes are made using wire compositions that are specifically geared toward an application. They contain no coatings other than those needed for the wire drawing. The purpose of the coding is to provide additional stabilizing on the arc, but has no other purpose. This type of electrode is used in welding manganese steel or other similarly composition materials.Light Coated Electrodes
These types of electrodes have a very specific and defined composition. The coating is applied on a surface by washing, dipping, brushing, spraying, tumbling, or wiping. The purpose of this coding is to improve the characteristics of the arc stream. This type of electrode serves three major purposes:- Greatly dissolves and reduces any impurities, such as oxides, phosphorus, or sulfur.
- Changes the surface tension of the molten metal. This ensures the globules of metal leaving the end of the electrodes are far smaller and more frequent. In doing so, this helps to make the flow of molten metal a lot more uniform across the weld.
- It helps to increase the arc stability by introducing materials that readily ionize.