Welding is an important part of many industries and can be incredibly satisfying to do. However, when your welder starts popping, your work can be brought to a sudden halt. Popping is a common issue that many welders face, and it’s important to understand why it’s happening and how to fix it. In this article, we’ll explore the reasons why your welder may be popping and the best ways to address the issue. We’ll also look at how to prevent popping in the future, so you can get back to welding without a hitch.
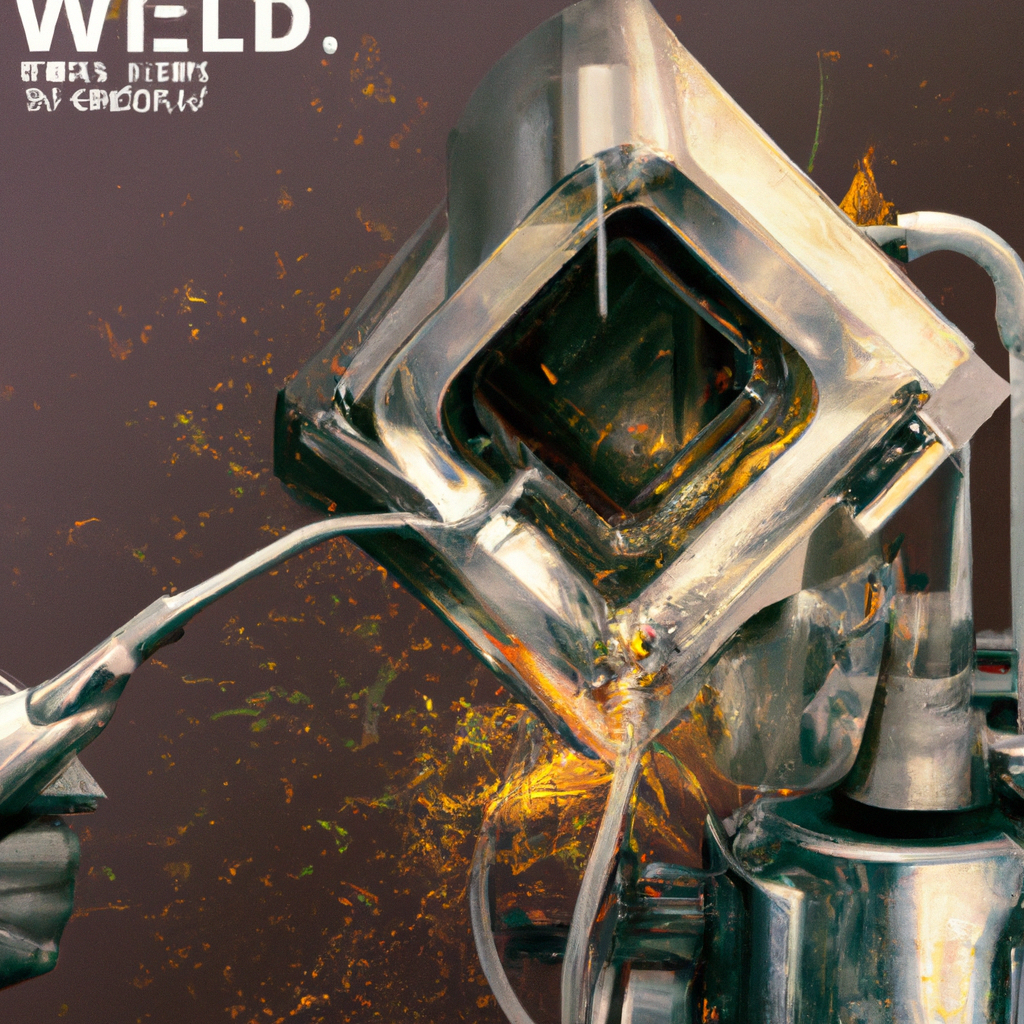
What type of welder are you using?
I am using a stick welder. Stick welders use a consumable electrode that is coated with flux, which helps to protect the weld from oxidation and contamination. The arc is created between the electrode and the metal being welded, and the heat generated melts the metal and the electrode to create a strong weld. Stick welders are ideal for welding in harsh environments, for repairing rusty metal, and for outdoor welding.
The popping sound you hear is called arc blow. Arc blow is caused by a magnetic field that is created when an electric current is run through a conductor. This magnetic field can cause the arc to deviate from its desired path, resulting in an uneven weld. To prevent this, the welder needs to be properly grounded, the electrode needs to be held at the right angle, and the welding current should not be too high.
Here are some tips to help reduce arc blow:
- Check the ground clamp and make sure it is firmly attached to clean, unpainted metal.
- Check the electrode holder and make sure it is tight and secure.
- Check the current setting and make sure it is not too high.
- Check the angle of the electrode and make sure it is held perpendicular to the workpiece.
Following these tips will help ensure that your welds have a strong and even finish, and will reduce the chances of arc blow.
What type of welding process are you using?
The type of welding process I am using is MIG welding. MIG welding, also known as Gas Metal Arc Welding (GMAW), is a semi-automatic or automatic process that joins two pieces of metal together by feeding a wire electrode along the seam. The wire melts and fuses the pieces together as it passes along the joint.
If your weld is popping, it is likely due to one of the following reasons:
- Incorrect wire feed speed: If the wire feed speed is too slow, the weld pool will cool before it has time to fully penetrate the joint. This can cause the weld to lack fusion and can cause it to pop.
- Incorrect voltage setting: If the voltage is too high, the weld pool may become too hot and cause it to pop. Conversely, if the voltage is too low, the weld pool may not be able to penetrate the joint properly, causing it to pop.
- Incorrect gas mixture: The shielding gas used in MIG welding must be properly mixed in order to protect the weld pool from contamination. If the gas mixture is incorrect, it can cause the weld to lack fusion and pop.
- Improper joint preparation: The joint must be properly prepared before welding in order to ensure a good weld. If the joint is not properly prepared, the weld may lack penetration and can cause it to pop.
These are the most common causes of welds popping. To ensure that your welds are successful, it is important to make sure that all of the above factors are properly set. Additionally, it is important to make sure that your welding technique is correct.
Are you using the correct welding parameters?
When your welding machine is popping, it is usually indicative of incorrect welding parameters. To get the best results, you should make sure that you are using the following parameters:
- Correct amperage
- Proper voltage
- Correct electrode size
- Correct polarity
- Correct travel speed
- Correct arc length
If any of these parameters is set incorrectly, it can result in poor welds, arc instability, and excess spatter. To ensure that your welding machine is set correctly, you should consult your manual or speak to an expert.
What type of welding wire are you using?
The type of welding wire I am using is a mild steel wire. This type of wire is commonly used for many welding applications because it can be easily manipulated and is relatively inexpensive. Mild steel welding wire is ideal for welding of thin materials such as sheet metal, as well as thicker materials such as steel plates.
However, it is possible for the mild steel welding wire to cause popping, or what is known as arc blow. This is caused by a combination of electrical and magnetic forces that cause the arc to be drawn away from the weld joint. Arc blow can be caused by a number of factors, such as:
- Incorrect electrode polarity
- Too long of an arc length
- Too high of an amperage setting
- Incorrect welding technique
In order to prevent arc blow, it is important to follow the manufacturer’s specifications for the weld, such as selecting the correct electrode polarity, setting the correct amperage, and using the proper welding technique. Additionally, it is important to ensure that the weld joint is clean and free of debris or contaminants. Following these steps can help to reduce the likelihood of arc blow and ensure a successful weld.
Is the wire feeding correctly?
There are a few reasons why your welder may be popping:
- The voltage is too high: The voltage is the first thing you should check if your welder is popping. Set the voltage to the correct setting for the type of metal you’re welding.
- The wire speed is too fast: If the wire speed is too fast, it can cause the wire to become erratic and cause popping. Adjust the wire speed so that it is in line with the type of welding being performed.
- The wire is not feeding correctly: If the wire is not feeding correctly, it can cause the wire to become stuck and cause popping. Make sure the wire is properly fed through the liner and check the feeding speed.
- The drive roll is worn out: If the drive roll is worn out, the wire may not be able to be fed properly and can cause popping. Replace the drive roll with a new one and check if the popping stops.
If none of these solutions fix the problem, it may be an issue with the power source or welding torch. In this case, it is best to consult a professional welder for help.
Are the electrical connections secure?
To ensure that the electrical connections for a welder are secure, there are several steps you can take:
- Check the input power cord for any damage. Replace if necessary.
- Ensure the power source is adequate for the welder.
- Check the ground connection. Make sure it is securely attached to the welder and to a ground source.
- Ensure the power cord is plugged in correctly and firmly.
- Check the welding cable connections for snugness.
If any of these steps have been overlooked and the electrical connections are not secure, it could be the cause of the welder “popping”. The popping sound could be caused by an arc or spark, which can be dangerous if the connections are not secure.
Is the ground connection secure?
When welding, it is important to make sure that the ground connection is secure. A secure ground connection will make sure that the current flows through the work piece instead of through the arc. If the ground connection is not secure, the current may not flow through the work piece, resulting in a “popping” sound. The “popping” sound is caused by the sudden release of energy as the current arches away from the work piece.
To ensure a secure ground connection, here are some steps you can take:
- Check for frayed wires or loose connections in the ground cable.
- Make sure the ground clamp is secure and making good contact with the work piece.
- Check to see if the ground cable is long enough to reach the work piece.
- Check the ground cable itself for any signs of damage.
If the ground connection is secure, but you are still hearing a “popping” sound, then the issue may be caused by something else. Make sure that the welding machine is properly set up and that the welding rod is the right size and type for the job. If everything is set up correctly, then the problem may be with the arc itself. Make sure that you are keeping the arc length consistent and that you are welding at the correct speed.
By making sure that the ground connection is secure, you can help ensure that your welding job is successful. Following the steps outlined above can help you make sure that the ground connection is secure and that your welding job will be successful.
Is the gas pressure and flow rate adequate?
When using a welder, it is important to make sure that the gas pressure and flow rate are adequate. If the pressure and flow rate are inadequate, the welder may have difficulty welding and may even start to pop. Here are some of the reasons why your welder may be popping:
- The gas pressure is too low – If the gas pressure is too low, the welder will not be able to create a strong enough arc, causing the welder to pop.
- The gas flow rate is too low – If the gas flow rate is too low, the welder will be unable to sustain a long enough arc, causing the welder to pop.
- The tip size is too small – If the tip size is too small, the gas flow rate will be too low, causing the welder to pop.
In order to ensure that your welder is working properly, it is important to make sure that the gas pressure and flow rate are adequate. The ideal gas pressure should be around 80, with a maximum of 120. The gas flow rate should also be adequate. If the gas pressure and flow rate are not adequate, the welder may have difficulty welding and may even start to pop.
Is the shielding gas correct for the material and process being used?
The shielding gas used is an important element in welding. It is important to choose the correct shielding gas for the material and process being used, as it can affect the quality of the weld and the safety of the welder. The wrong shielding gas can lead to the welder popping, which is when the arc is extinguished, due to inadequate shielding.
In order to determine if the shielding gas is correct, some factors should be taken into consideration:
- What material is being welded?
- What process is being used?
- What type of shielding gas is being used?
- What is the gas flow rate?
The shielding gas should be chosen based on the material and process being used. Different materials require different shielding gases, and the process being used will affect the flow rate of the gas. For example, for mild steel, a 75/25 mix of argon and carbon dioxide is typically used, while for stainless steel, a 100% argon mix is used. The flow rate should be between 80 and 120 liters per minute.
If the wrong shielding gas is being used, the welder will pop. It is important to ensure that the correct shielding gas is being used in order to ensure the safety of the welder and the quality of the weld.
Is the welding gun clean and free of contaminants?
It is important to keep your welding gun clean and free of contaminants for it to perform at its best and to prevent any unnecessary issues. Here are a few things to check for if your welder is popping:
- Check the tip of the welding gun to make sure it is not clogged with dirt or debris.
- Check the power cord and the connections to the welding gun to make sure everything is securely connected.
- Check the air pressure of the welding gun to make sure it is set to the correct pressure.
- Make sure the welding gun is free of oil, grease, or other contaminants.
- Check the wire feed rate to make sure it is set to the correct rate.
If your welding gun is clean and free of contaminants, it should produce a smooth and consistent arc. If you are still having issues with popping, it may be due to a faulty welding gun or other component. In this case, it is best to consult a professional to assess the problem and recommend a solution.