When Many Types of Welds Can Be Used
In addition, there are many materials where the welder can use several different kinds of Welds and still get a great look and joined. Cast iron is one such example, where this material works very well with several different types of welds and is one of the reasons why it is a very commonly welded material. This is not true of every kind of material you will use, however. You are going to find that there are certain types of metals or metal compositions where only one or maybe even two types of welds can be employed. Any other kind of weld can cause serious issues.Which Budget Wire Feed Welder is Best for Welding Different Metal Compositions?
Looking for the best budget wire feed welders to handle different metal compositions? Look no further! Our top picks are equipped with advanced features, ensuring smooth and precise welding on various metals. These welders are budget-friendly without compromising on performance, making them ideal for all your metal welding needs.
Testing the Composition
When you are assigned were hired to do a welding job, there may be instances where you are unsure of the metal composition. Unfortunately, this happens a lot more frequently than you may imagine. However, there are tests you can perform that can assist you on determining the composition. The chart below provides a list of base metals and their alloys, as well as some of the indicators that tell you about the composition of the metal.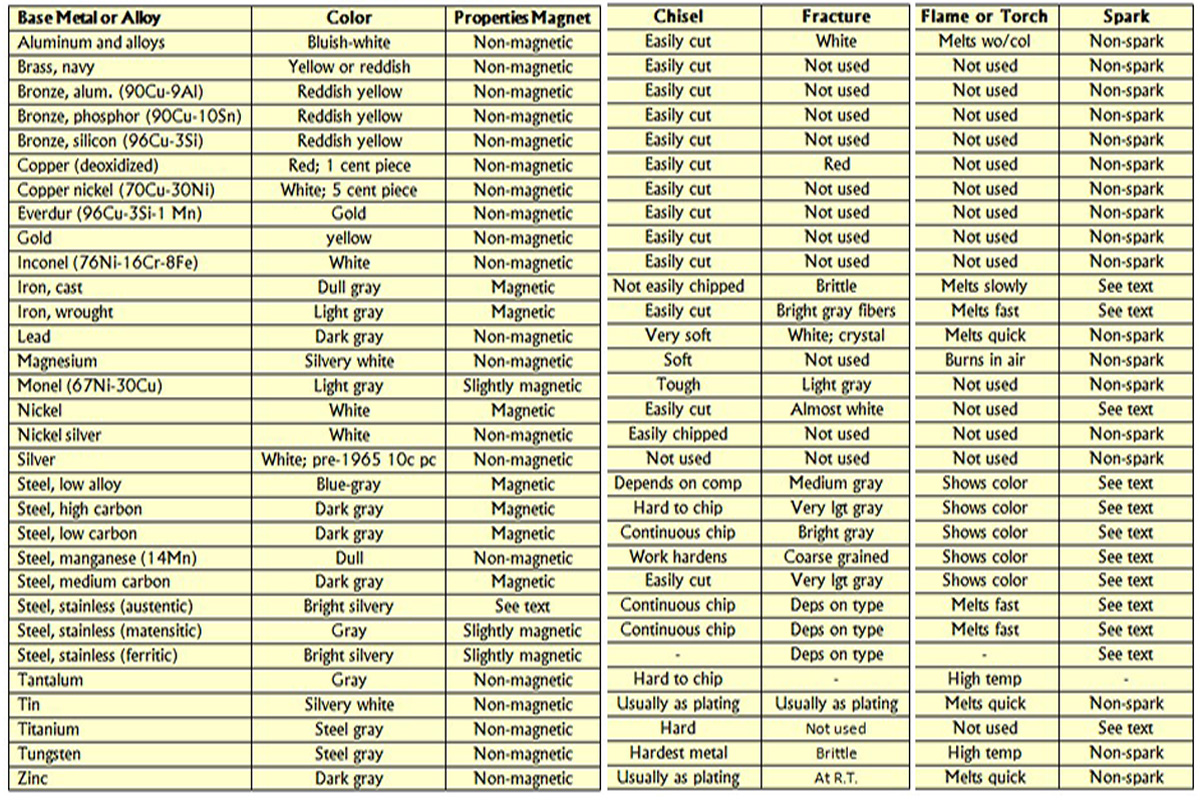
Test #1: Appearance
The first test that is to be performed is related to appearance. Things such as color and the appearance of the surface tell you a lot about what kind of metal composition you have. If you look at the shape it will also give you clues for example, looking at bumpers to cars, beams, pipes, and pipe fittings will tell you a lot about the material used, because only certain alloys can be molded in this way. An example of this would be a pipe. Cast iron is one of the few materials that can be molded and shaped in this way to provide you with a pipe. This distinguishes it from magnesium, aluminum, and brass. If the metal is oxidizing is another way to tell. If so, then its color will have a different shape, such as when rust forms on a surface. If you notice that there is rust on a material made of steel, then it is not going to be made of carbon steels.Test #2: Fracture
You can tell a lot about the composition of the metal by studying broken pieces of that metal or by chiseling off chips from the metal and studying them. This will allow you to see the color of the base metal before it has gone through the oxidation process. For surfaces like magnesium, copper, and led, the roughness of a broken surface is one of the clear indicators that one of these three metals has been used. If the material is easy to mold or band, referred to as ductility, this will tell you about the metal. Some metals will not bend it all over are extremely brittle. These are the kinds of things you would look for and compare in the charts presented above.Test #3: Spark
If the metal produces a spark when held against the high-speed grinding wheel is another way to test the metal composition. While this test is not a replacement for chemical analysis, it is a quick and easy method to tell you about the types of metals that may be used within your material. When pressed against one of these high-speed grinding wheels, iron and steel will produce sparks. They also very in the length, color, and shape of the spark that is produced. This is an indicator of whether you have steel or iron as part of the metal composition. To perform this test, it is important to be in a darkened room where you can make a full analysis of the color of the sparks. Too much light can distort this, creating a false impression of the metals used.Test #4: Torch
The next type of test uses an oxyacetylene torch. By identifying how quickly the metal melts, producing a puddle of molten metal and slagged, one is able to figure out what the chemical composition may be. The color will also change during the heating process. Here is what to look for in helping you to determine the type of metal composition:- Aluminum. If aluminum is the material, you will see a minimal amount of melting at best. Aluminum has a very high connectivity, making it so that the metal does not melt when a heat source such as a torch is applied to it.
- Zinc. If the metal contains anything, a sharp corner will melt quickly. This is because zinc is a terrible conductor.
- Copper. Copper will eventually melt, but not quickly. Copper alloys that are composed of led will begin to boil.
- Magnesium. When magnesium burns, it gives off a sparkling white flame.
Test #5: Magnetic
Most of us recognize that metals are magnetic. If you have a small magnet, you are able to test to see if there is enough of a composition of metal to produce a magnetic effect. Materials that are strongly magnetic include carbon and low-alloy steels, iron alloys, stainless steels, and pure nickel. In some instances you may get a slightly magnetic reaction. This occurs in high-nickel alloys and stainless steels made of 18 chrome, eight nickel type. Non-met Amanda materials include such things as zinc based alloys, magnesium, aluminum based alloys, copper based alloys, and precious metals.Test #6: Chisel
The chisel test can act as a great indicator for you. In this case, the only thing that you need to perform this test is a cold chisel and a banner. Use the chisel to hammer on the edge or corner of the material whose metal composition you are looking to check. If it is easy to chip away at a small portion, this is a clear indicator of the hardness of the metal. If you are able to continually chip at the material and the chip continues, you have a ductile material. Common materials that will act in this way include mild steels, aluminum, and malleable iron. If the chips break apart easily, then you have a very brittle material. Cast iron is one such example of a material that will break apart easily. Four materials made of high-carbon steel, you’re going to find that ships are extremely difficult to produce.Test #7: Hardness
The chart below provides information about the hardness of metals.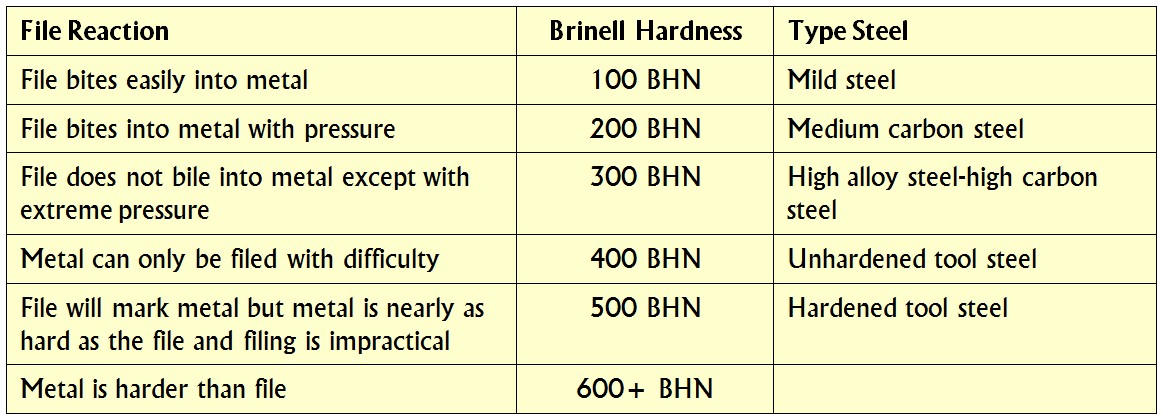