Understanding Weld Types
Before talking about the specific types of welds, it is important to understand what separates one weld from another. The primary factor is the shape of the weld when viewed from a cross-section. This shape is the most significant factor, and is the primary indicator for such welds as seam, surfacing, backing, plug, slot, fillet, cross-sectional, and flange. From there, the next thing to consider are the types of joints that are made using the well. There are five different main types of joints, which include the following. Examples of these joints are shown in the diagram.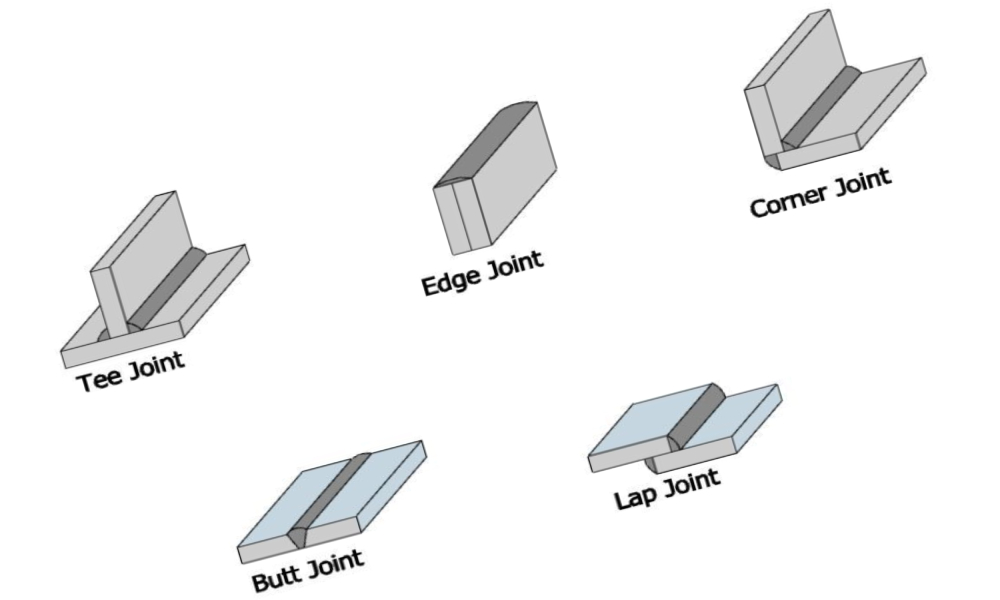
- Butt joints
- Corner joints
- Edge joints
- Lap joints
- Tee joints
#1 Fillet Welds
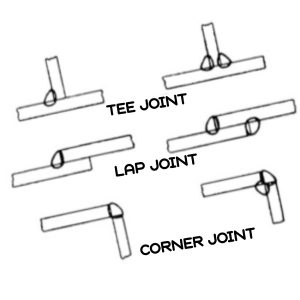
- Full fillet weld. In this case, the size of the weld is approximately the same thickness of the thinnest object that is being joined by the weld.
- Staggered intermittent fillet weld. In this type of weld, two lines of intermittent welding are created on a joint. An example of this might be a tee joint, where the increments of the weld are staggered down the length of the weld, with some of the weld created on each side of the tee.
- Chain intermittent fillet weld. In this type of weld the intermittent fillet welds are approximately opposite on one line than they are to the other.
- Convexity. This is a term that refers to the maximum perpendicular distance from the face of a convex fillet weld to the line which joins the toes.
- Boxing. This term refers to the continuation of the fillet weld as it goes around the corner of the material. This is an extension of the principle weld.
#2 Groove Weld
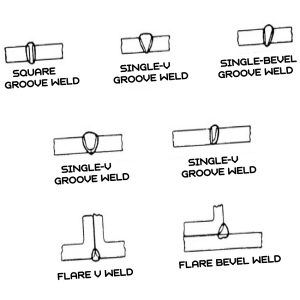
#3 Surfacing Weld
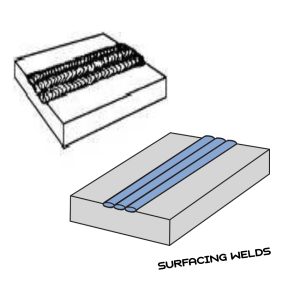
#4 Flash Weld
The flash weld gets its name from the resistance welding process that is used in the well. Fusion is produced over the entire abutting surface. This heat is created by the resistance generated to the current flow between the two materials that are being combined. By applying pressure coupled with the heat, it creates a quick joint, thus getting its name.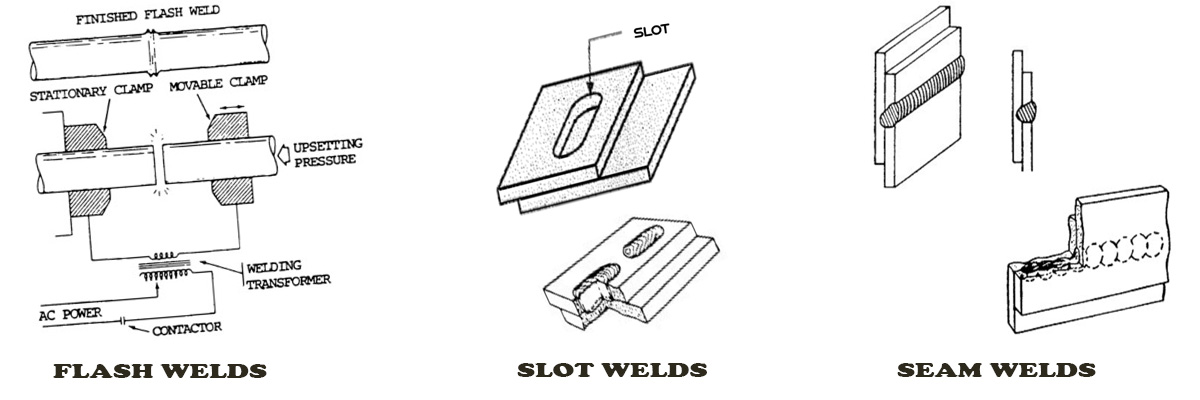
#5 Slot Weld
This type of weld is made in an elongated hole in one of the materials that is used. A lap or tee joint is created between the two services. The weld is then created at the point where the exposed hole is located. The hole could be open at one end or it could be partially or completely filled by the weld material.#6 Seam Weld
This type of weld is made by the arc seem or the resistance seam welding. During the welding process a resistance seam weld is generated. This type of weld often gives the appearance of a seam, like you would see in clothing.#7 Plug Weld
These are circular welds that are created through one material. This allows for a lap or a tee joint to be created to the other member. In this way, it looks very similar to using a screw or bolt to lock two pieces of material together. In fact, this weld is often used in the place of rivets.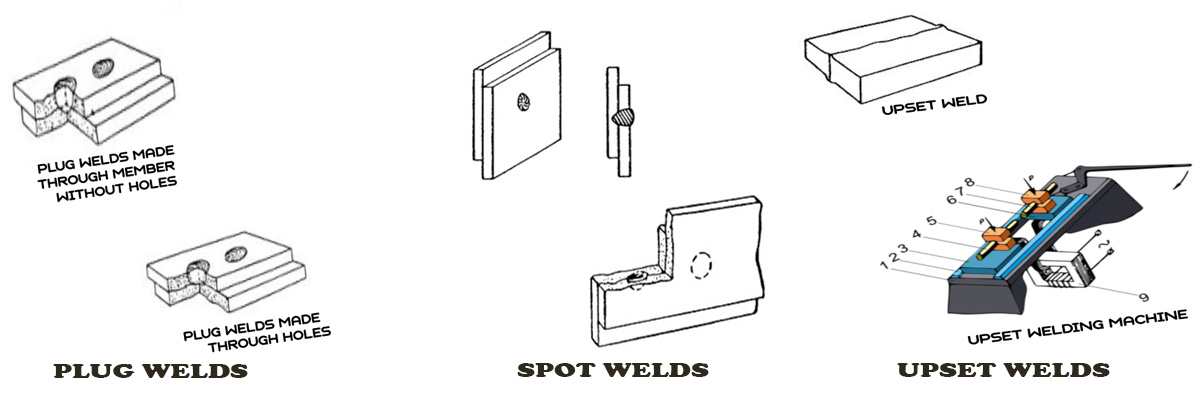
#8 Spot Welding
This type of weld is created by an arc spot or resistance spot weld. This type of weld gets its name from the inference that a resistance spot weld is created.#9 Upset Weld
In this type of weld, fusion occurs progressively along the area of the joint. This fusion covers the entire abutting surface. Pressure is absolutely necessary to help create this type of weld, and it must be maintained during the entire heating period.Which Welding Metal is Best for Different Types of Welds and Joints?
Different types of welding metals are better suited for specific types of welds and joints. For instance, steel and stainless steel are commonly used for structural welds due to their strength and durability. Aluminum, on the other hand, is preferred for lighter applications. Additionally, specific alloys like titanium or nickel-based metals are chosen for specialized welding projects that require corrosion resistance or high heat tolerance. Choosing the right welding metal is essential to ensure the integrity and longevity of the welds and joints.
Welding Positions
To close out this article, we wanted to spend a little time talking about the different welding positions. Welding positions refers to the position of the structure during the welding process. Because some positions are tricky or provide obstacles to free access, techniques have been developed to help in the welding process.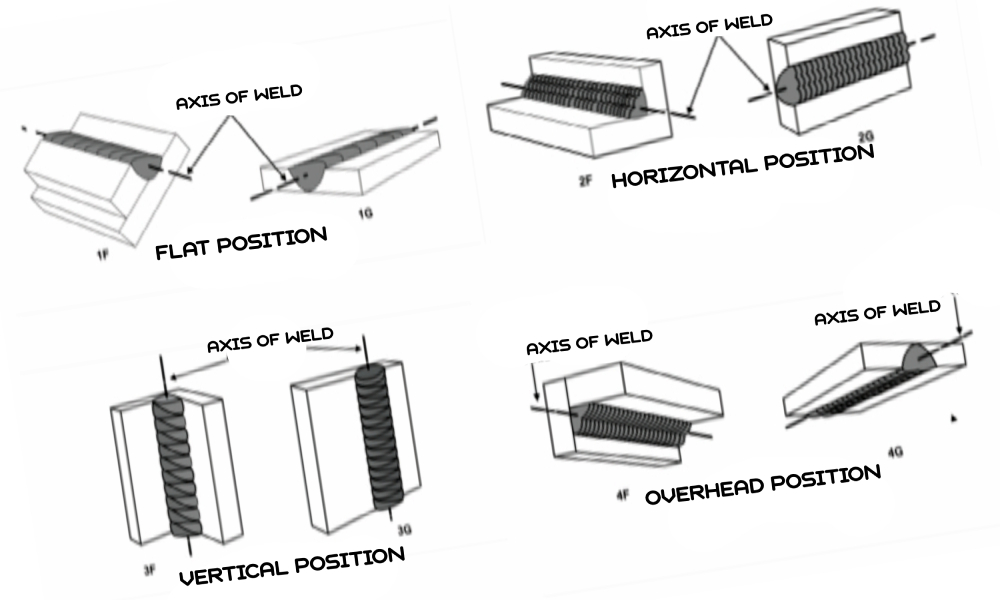